Have you ever gone on the search for a new ERP-software system for your metal fabrication business?
If so, you know that it is difficult because there are many vendors out there all claiming they have the perfect solution, but you also hear about the horror stories of failed implementations.
So, what do you do?
Many people have been able to find success by starting out with an early independent analysis of ERP software systems, such as this guide.
Before you buy and implement an ERP system, there are a few things you should know to make sure the project doesn't result in frustration, or worse- a failed project.
To help you get started, I've created an independent and personally curated comparison of the top 10 ERP systems for metalworking and sheet metal fabrication. It not only draws inspiration from solutions but also helps you ask the right questions.
It’s best suited for contract manufacturers, job shops, and more discrete make-to-order environments. However, if you’re in more continuous/batch production or work at scale, feel free to reach out, and I can assist.
I'm convinced this selection guide will help you choose the option that will increase your business's efficiency in the short term and for the years to come.
So, without further ado, let's dive in!
The Top 10 List Of 2025
As of the update date, I believe the following are excellent solutions that can support your business processes and more:
Software | Provider | Product Information | Region |
---|---|---|---|
ECI Ridder iQ | ECI Software Europe | Ridder iQ | Europe |
Microsoft Business Central | Microsoft | Business Central | Global |
Odoo | Odoo | Odoo | Global |
Fulcrum Cloud | Fulcrum | Fulcrum Cloud | Global |
ECI JobBOSS² | ECI Software Solutions | JobBOSS² | Global |
ECI Bemet | ECI Software Europe | Bemet | Europe |
Infor M3 | Infor | Infor M3 | Global |
MKG 5 | MKG | MKG 5 | Europe |
Genius ERP | Genius ERP | Genius ERP | USA, Europe, Australia |
MRPeasy | MRPeasy | MRPeasy | Global |
Modern ERP for Fabricated Metals
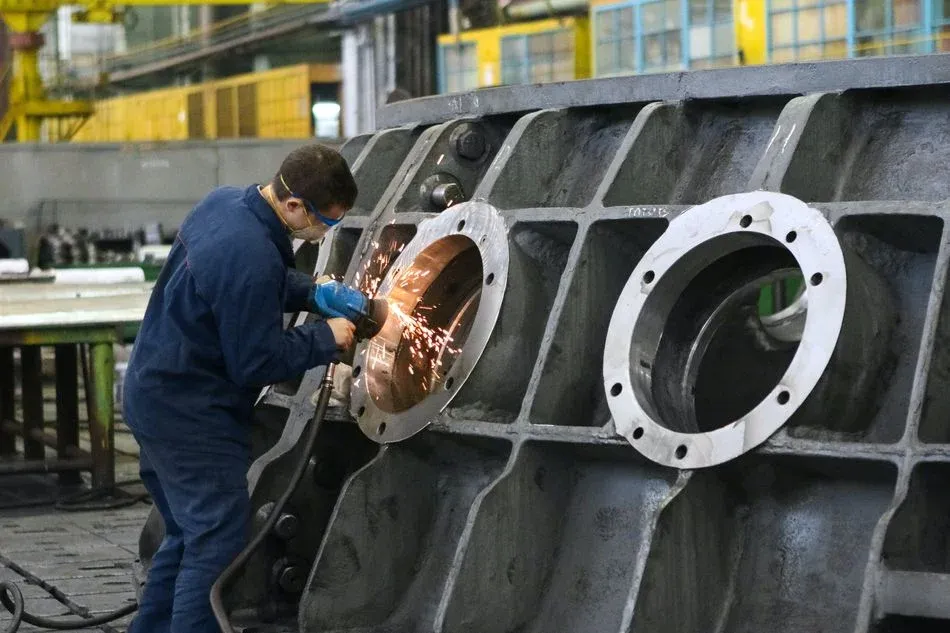
As global supply chains become more complex, the fabricated metal industry must find efficiencies in new technologies and processes.
Traditional practices have proven to be inefficient with the increasing level of complexity within these global supply chains.
Already thin margins are being further threatened by rises in raw material costs, shorter product lifecycles, and more stringent quality standards.
Many organizations are looking to adopt lean initiatives to bring down costs, reduce waste, and realize efficiencies across their complex supply chain to remain profitable. This might not be enough, though, and that's where modern ERP for fabricated metals manufacturers comes in.
ERP is an integrated, powerful suite of software for an organization's operations. It helps the organization to manage its workflow and help automate many processes.
What are the benefits of metal fabrication ERP software?
An ERP software for metal fabrication can provide many benefits. It can help with production and inventory management, which in turn will lead to a better utilization of resources and a more profitable business.
A metal fabricator who installs modern ERP software correctly can increase production output and without having to hire more staff. This will make it easier for the business to grow and be more efficient with operating costs.
It provides better inventory management and control, which makes it easier to forecast finished products. It also streamlines production planning and gives businesses more overview and control of their operations.
Do you want to read more on ERP systems in general? You might also want to check out our other article: Why Enterprise Resource Planning (ERP) is important for metal fabrication
What are the must-have software components for metal fabrication?
Metal fabrication is a form of discrete manufacturing. It’s a manufacturing practice that operates with bill of materials (BOM) to make individual parts of a product. The pieces are then often merged to form the final product at the end of production.
Therefore, metal product manufacturers face some unique challenges in their production units due to BoM's and routes that are typically only partially defined, and a strong engineering function that governs product design.
There is usually a low-volume, high-mix approach, which requires data entry to be swift and ideally automated. For high-volume manufacturing, for example for cost-competitive laser centers, it is typically a challenge to deal with correct inventory levels, both in materials and finished products.
Planning to achieve shorter lead-time items and ensuring work is scheduled through the production facility in a timely and efficient way are key to success in this sector.
The right ERP software can help you save time and energy, as well as drive your success as a company. But why should you choose an ERP software over other alternatives? To answer this question, we must first know what the requirements are for a good choice.
Below, we’ve listed modules that we consider as must-haves and recommended:
Must-have modules for metalworking:
- Bill of Materials (BOM) and routing, often with support for Assembly structures.
- Material Requirements Planning (MRP)
- Customer Relationship Management (CRM)
- Sales and Purchase order processing
- Basic inventory management (raw materials)
Tip: Make sure your BoM allows you to create relationships between materials and operations. If it doesn't, you will have trouble creating integrations with your CAM-software.
Optional but recommended modules
- Product configurator and Product Data Management (PDM)
- Purchase requisition
- Pricing and quoting
- Shop floor control
- Time and attendance
- Financial management
- Enhanced Inventory Management (both finished parts and materials)
- Part tracking and traceability
- Quality Assurance / Quality Control
- Production Management
There are, of course, many more modules. For example, vendors often combine their ERP-offering with Manufacturing Execution Systems (MES).
This can be tricky, since there can be quite some overlap in functionality between ERP and MES. In general, it might be wiser to look for these features later down the line. When in doubt, contact us, and we can discuss your particular situation.
How to select the right software for you
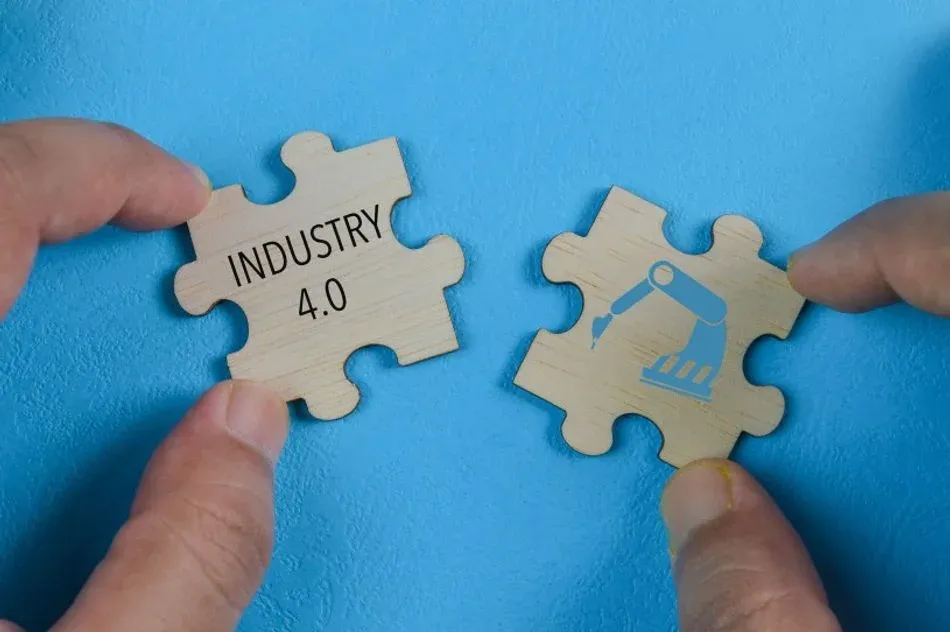
Factors to consider when choosing ERP System for metal fabrication
One of the major factors in choosing an ERP is its pricing. It must be in line with the budget allotted for the purchase and set-up costs. Another factor to consider is whether it is flexible enough to accommodate changing requirements in business operations. Being able to customize your experience can be vital in this regard.
The software should also be easy to learn and use, or else it will only add to the existing office and production bottlenecks. Finally, make sure that accurate data flows unhindered through all stages of your company. If the software is very compartmentalized into separated software modules/databases, it will probably be hard to create a good collaboration in your business.
Tip: Any good ERP-software maker should let you try out their solutions, whether on a demo instance or a trial account. This is important because you need to experience how the flow of the system is and if it works right out of the box. A lot of customization up front is usually a red flag.
Cloud, Hybrid Cloud or Native Cloud?
With the advent of digitalization, more and more companies are moving their data to the cloud. But, there are many benefits and drawbacks of both types of cloud.
- On-premise solution: Installed on PCs and connected to a server in your business. Usually, a robust solution, but requires server specifications and maintenance. Can be complicated with multi-factory or multi-site solutions.
- Hybrid Cloud: Installed on PCs and connected to a server hosted by the vendor (externally). Commonly used for multi-factory solutions, less recommended for single-factory solutions. Performance is often slower than On-premise.
- Cloud (Native): No installations necessary, software is running from your web browser. Can be used by single and multi-factory solutions, and often has exceptional performance when designed well. Typically, requires on-premise integrations with other software such as CAM, MES, and CAD.
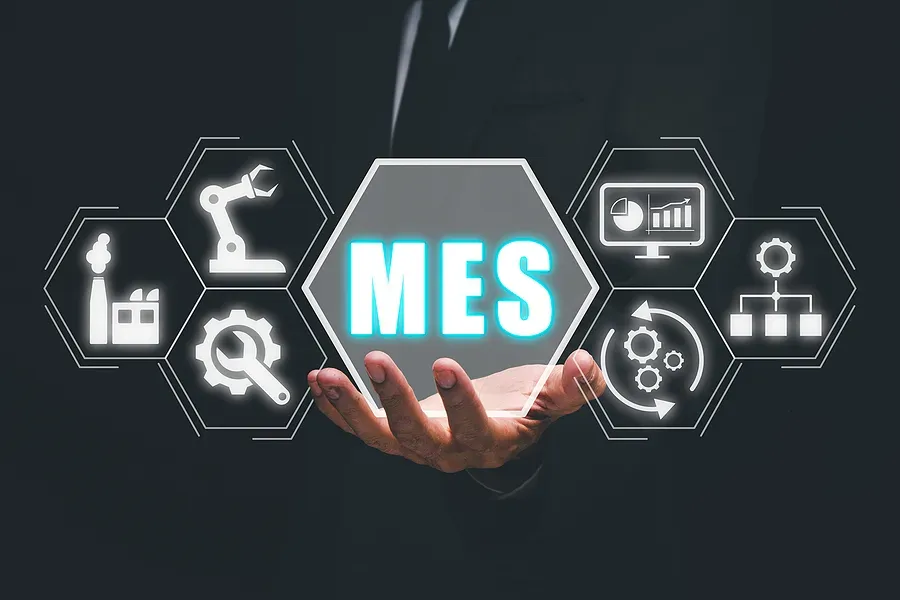
Integrations and app exchanges
It's not common for your company to only work with ERP software; there is typically CAD, CAM, and MES software in your business. It has been shown repeatedly that integrating such solutions is crucial for the long term success of your implementation.
In our selection, we therefore look for systems that are easy to integrate. The easiest way to do this is if the vendor provides an API and an app exchange. Below are a few selection criteria you could consider.
To make integrations easier, look for :
- Are there off-the-shelf integrations for your software systems?
- Is there an API that is well documented?
- Does the company provide an app store?
- Does the company have a proven track record in your industry?
- Do they provide their own consulting, or are you dependent on third parties?
What integrations do you usually need?
Common integrations needed:
- CAM-integration, for example, the programming software of your machine
- MES-integration, for example, your machine job manager
- CAD-integration, for example: SolidWorks, Inventor, CATIA, etc.
Tip: Ensure you speak to your vendor about API-connectivity and the cost of this, so you can easily connect other apps or built your own. While not necessary, some great bonus features of great connectivity are the ability to import CSV, XML and JSON files, so you can import customer orders directly in your system.
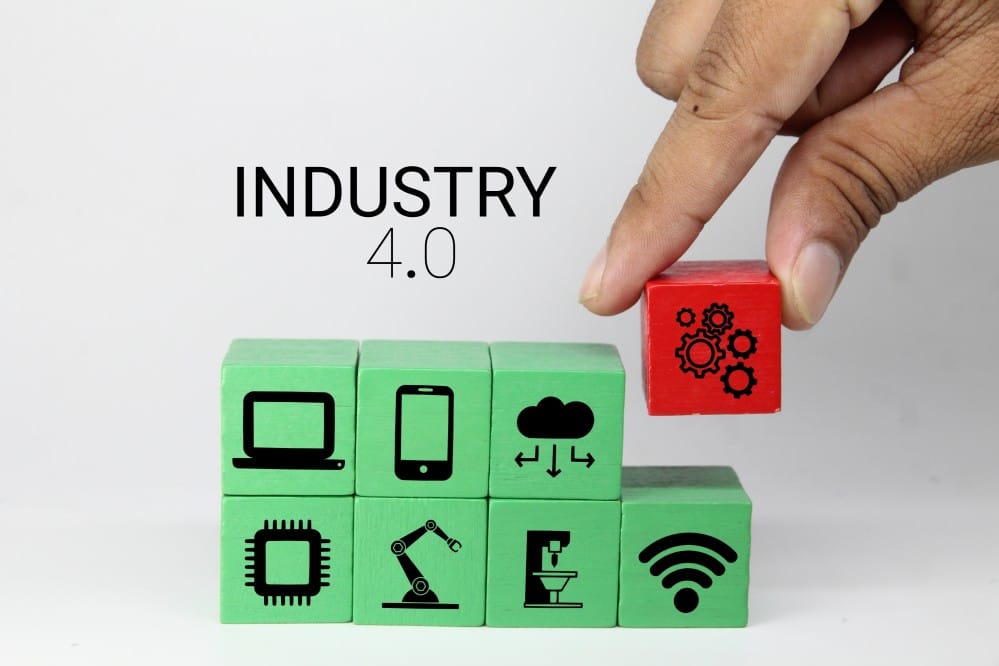
Regional / local support
Can your software providers comply with your local and customer regulations and quality requirements for quality and security purposes? For example, think about data protection (GDPR), but also quality standards such as ISO 9001.
It's not uncommon that countries or even states have vastly different requirements. If the software company does not have insight into the local requirements, you might be up for disappointment.
It is important to always be mindful of the safety concerns involved when it comes to selecting computer software. The best way to ensure you are playing it safe is by seeking a partner network that is global and trusted, and hiring a specialized third party with knowledge on the latest advances in technology.
Tip: Make sure your vendor has a 24-hour support service, so you can always reach them in case of an issue. Whether you're working through a reseller or directly with the provider, you must make sure that your system comes with good personal service.
Do they understand your shop?
Many software solutions are not designed in workshops, but are instead designed by financial departments or for large enterprises. This can create friction when your daily smart work methods are not there from the start. Especially when you consider metal fabrication to be such a specialized industry.
Changing a generic product for a customized one is usually an expensive undertaking that most manufacturers and fabricators can't afford.
Therefore, it makes sense to question whether the product has been developed at, by, or in collaboration with your industry.
In case you're choosing a generic product, make sure that there are specialized partners and providers for your industry. In the comparison below, we will pay extra attention to this factor.
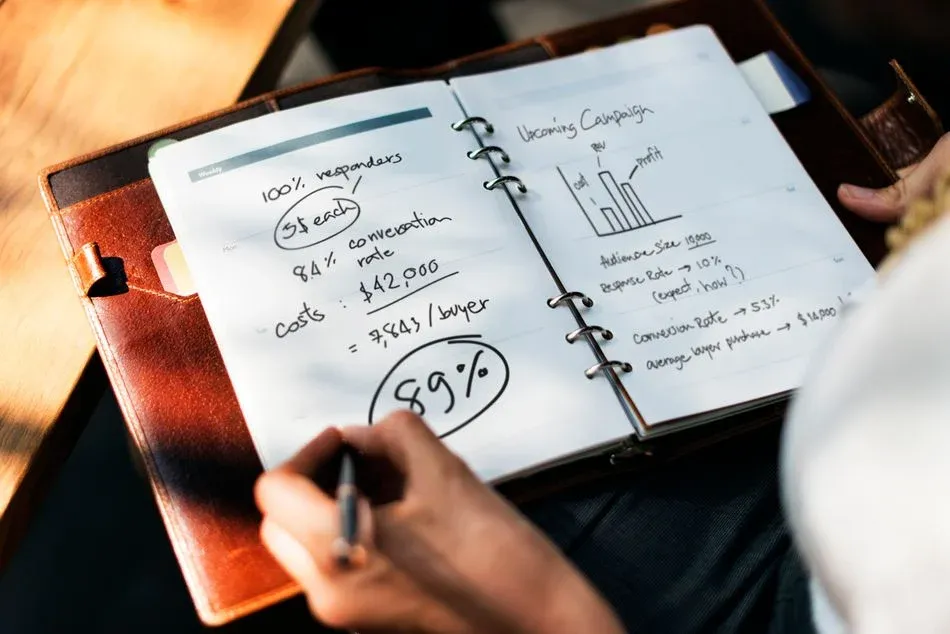
Quick Guide to 10 Best ERP Systems in the Market
Today, there are many ERP software solutions available in the market. It’s challenging to make an informed decision. In this article, we have compiled a list of 10 best ERP solutions you should take a look at.
The 10 Best Metal Fabrication Software Systems
1. ECI Ridder iQ
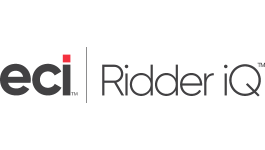
Overview
Ridder iQ is a modular ERP system built for manufacturing, designed by ECI Software Europe (previously Ridder Data Systems). It focuses on production management, planning, and shop-floor control, especially for metal fabricators and machinery builders.
I've personally guided over 10 clients through their go-live on this platform, and I believe it remains the undisputed winner in terms of flexibility, integration, user interface, and feature richness. Curious if this is the right choice for you? Consider a strategy call.
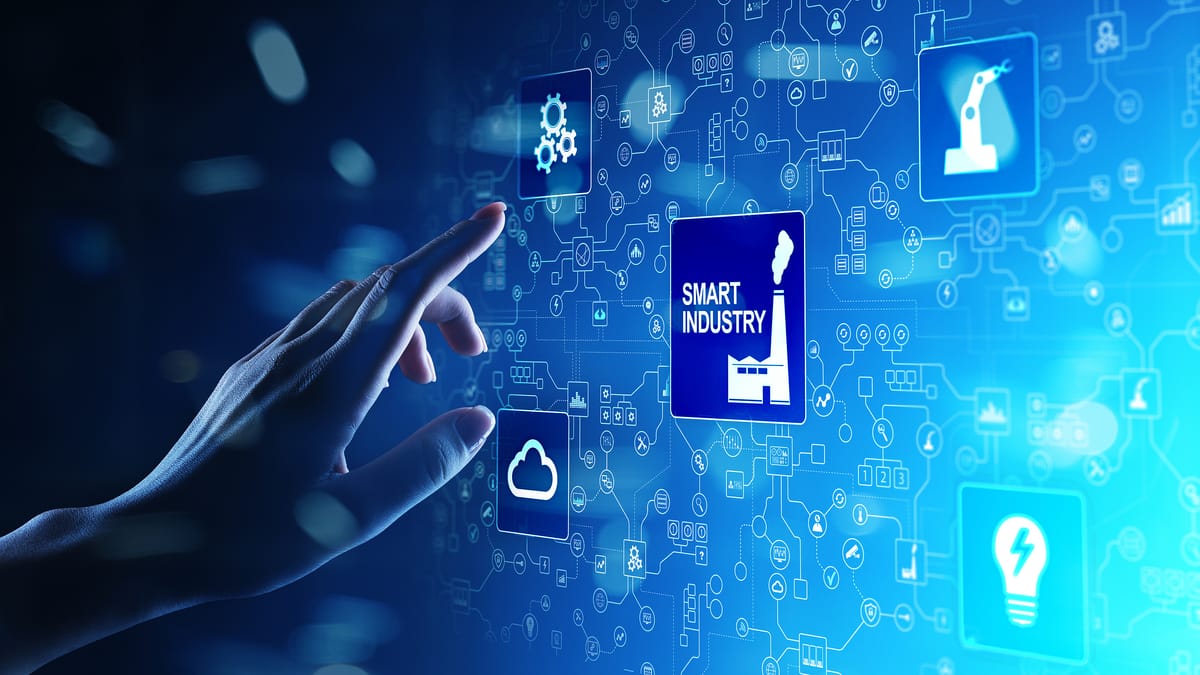
Key Strengths
- Modular Structure: Tailor specific modules to company needs.
- Production Insights: Full support for inventory, job tracking and scheduling features.
- Extensive scripting: You can customize any table, script, workflow and lately also comes with a full web API.
Resources
- Website: Ridder iQ
- Video: Ridder iQ Demo
- Additional Info: SourceForge
2. Microsoft Business Central
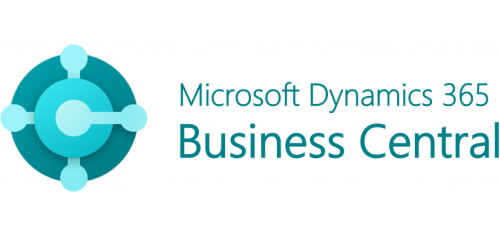
Business Central is an emerging cloud-based ERP solution from Microsoft's Dynamics 365 suite. It integrates seamlessly with familiar Microsoft tools like Office 365 and Power Platform, making it suitable for mid-to-large organizations seeking a broad feature set.
There is a lot of hype about the AI copilot functions, which allow you to automate order entry, summarization, draft messages, and much more—something to keep in mind.
I've had excellent recent experiences with the implementation paths when handled correctly. There are hundreds, if not thousands, of apps available, there is a solid API and you can script extensively. However, the product can be pricey if not managed well.
Note: The software is generic, meaning it won’t include any metal fabrication templates out of the box. Microsoft has large reseller network, and the quality of the implementation will depend on that. There are also various industry template apps, such as BySoft Business and Metal Manager, among many others. However, these may limit your flexibility in the long run.
Considering implementing BC?
To avoid having to explain and reinvent the wheel with your partner, I highly recommend getting expert guidance, such as in my digital factory program. This will save you months on your timeline.
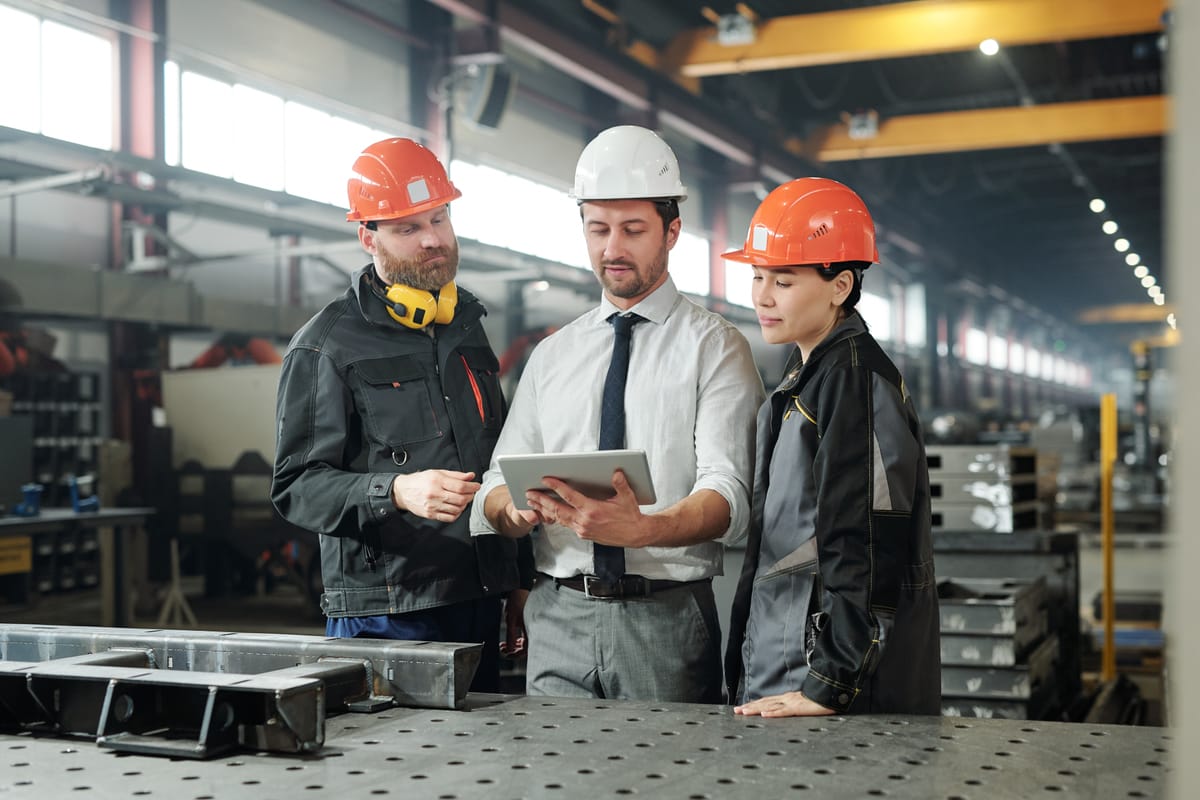
Key Strengths
- Integration: Strong connections with Outlook, PowerApps, and Teams, plus extensive AI features.
- Robust Reporting: Flexible drill-down capabilities for financial and operational data.
- Global Reach: Extensive worldwide partner network for implementation and support.
Potential Considerations
- Licensing costs can increase quickly if many users need full access.
- Some features, like marketing automation, may require additional apps or third-party tools.
- You will likely hear more about the AI features, which are impressive, but take them with a grain of salt in day-to-day usage.
Resources
- Website: Microsoft Business Central
- Video: Business Central Overview
- Reviews: Capterra | G2
3. Odoo
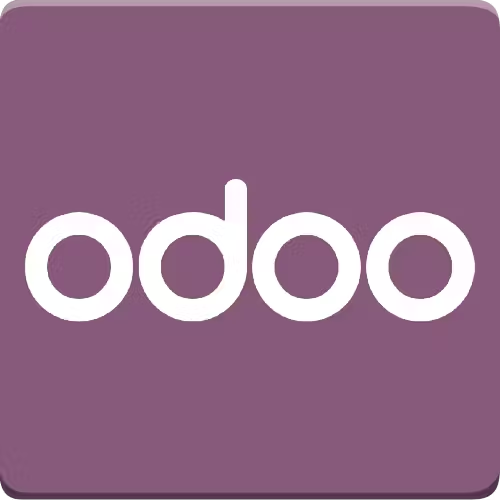
Overview: Odoo is an open-source ERP platform offering a suite of applications, from accounting and manufacturing to CRM and e-commerce. Its modular approach lets businesses deploy only the apps they need.
Odoo is the ultimate Swiss army knife of business software, enabling any business process imaginable, from sales to HR, finance, and even managing your website, social media, and WhatsApp texts.
Like Business Central, it's generic, offering maximum flexibility at the expense of depth in certain areas.
However, Odoo excels in ease of customization and integration. In fact, you can even use it for free and self-host it. Any small shop serious about digitalization should consider exploring it.
Where to start with your project? Consider a (remote) training:
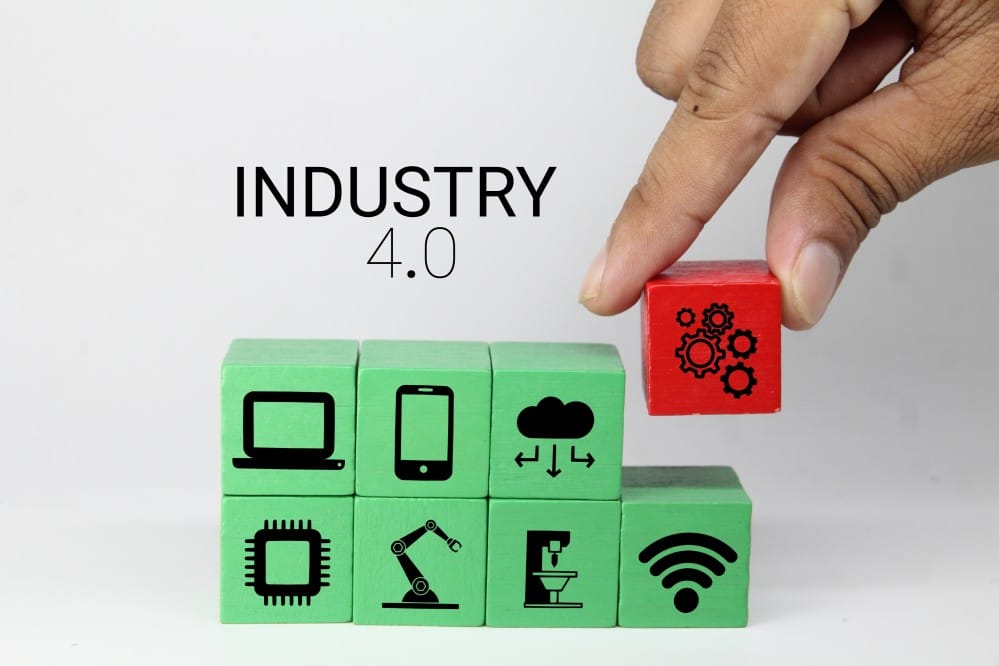
Key Strengths
- Open-Source Flexibility: Highly customizable with a large community.
- Wide App Library: Covers CRM, MRP, HR, and many industry-specific add-ons.
- Modern UI: Generally praised for a clean interface and rapid feature updates.
Potential Considerations
- Advanced custom reporting often requires developers.
- Free plan is limited to a single app; additional modules require paid licensing.
Resources
4. Fulcrum Manufacturing Cloud
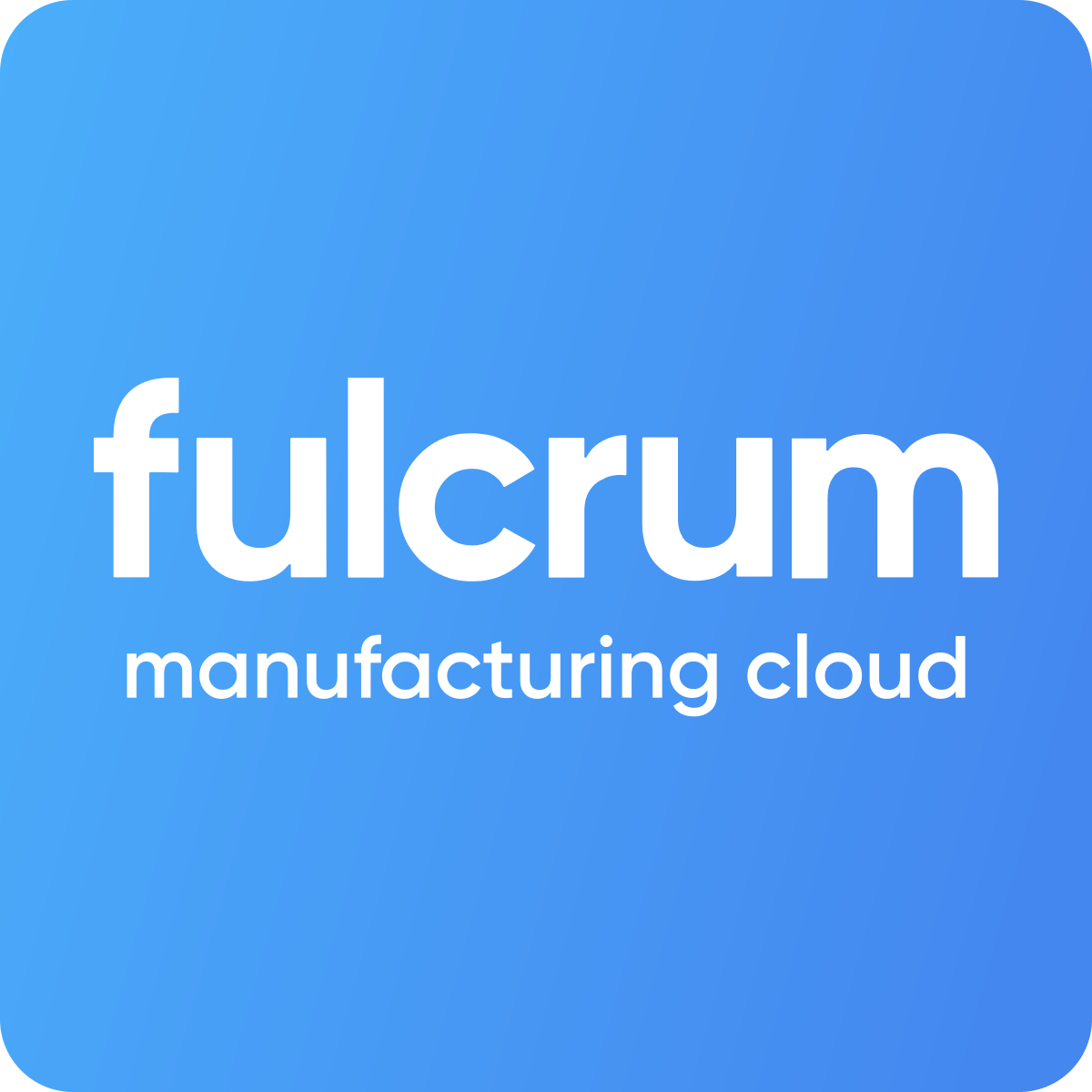
Fulcrum is a modern, cloud-native ERP designed for small to medium manufacturers, emphasizing real-time data, scheduling, and workflow automation. It is particularly popular among job shops and custom fabricators.
Currently (as far as I know), it is only available in the US and Australia. The project has significant potential and is especially beneficial for those seeking a ready-to-use turnkey system.
It features a modern API and supports various integrations. Their 3D shopfloor apps are state of the art. However, customization of the system is fairly limited.
Key Strengths
- Real-Time Production Tracking: Helps reduce manual updates and delays.
- Scheduling & Job Tracking: Highly visual scheduler and job boards.
- Strong Support: User reviews often highlight responsive, friendly technical help.
Potential Considerations
- Occasional slow load times reported.
- Some features (e.g., advanced invoicing) may still need workarounds.
Resources
- Website: Fulcrum
- Video: Fulcrum Preview
- Reviews: Capterra | G2
5. ECI JobBOSS²

Overview
JobBOSS² is a cloud-based shop management software from ECI Software Solutions, geared toward custom manufacturing. It includes tools for quoting, scheduling, labor tracking, and more.
Key Strengths
- Easy to Learn: Users praise its intuitive interface and rapid staff onboarding.
- Customization: Flexible data fields, plus optional QuickBooks integration for accounting.
- Comprehensive Shop Tools: Production scheduling, order tracking, shipping, invoicing.
Potential Considerations
- Customized reporting sometimes requires extra fees.
- Can’t fully delete obsolete data, which may clutter the database if not managed carefully.
Resources
- Website: JobBOSS²
- Video: Tutorials Playlist
- Reviews: Capterra | G2
6. ECI Bemet
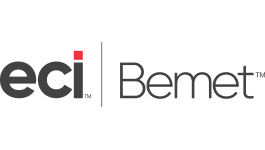
Overview
Bemet (formerly Plan-de-CAMpagne, acquired by ECI) targets mid-sized metal fabricators needing ERP and MES solutions under one roof. Their Plan-de-CAMpagne product is well-known in Europe.
Key Strengths
- MES Integration: Good synergy between planning, production, and shop-floor operations.
- Mid-Sized Focus: Designed specifically for job shops and manufacturing SMEs.
- European Base: Strong adoption in the Netherlands and surrounding regions.
Potential Considerations
- Users have reported inconsistent support integration after ECI’s acquisitions.
- Ensure vendor support is lined up for custom features or expansions.
Resources
- Website: ECI Bemet
- Video: Bemet Demo
- Reviews: Software Advice | Capterra
7. Infor M3
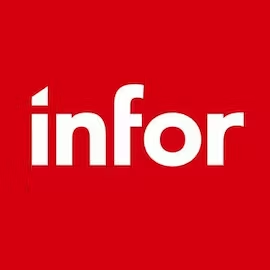
Infor M3 is a comprehensive ERP for larger manufacturers and distributors, covering finance, supply chain, production, and more. It’s highly configurable and often used in complex multinational scenarios.
I've seen some larger multi-site factories succeed with this, especially with their integrated solutions. However, like many other ERPs, it is more generic, requiring you to be thoughtful about your desired outcome, so a clear strategy is highly recommended.
That said, the system is highly scalable and suitable for even the most complex businesses.
Key Strengths
- Customization: Broad set of parameters to shape the system for unique processes.
- Stability: Known for reliability when configured correctly.
- Strong Support Community: Active user groups and Infor events/training.
Potential Considerations
- Complex setup can cause confusion if your team isn’t well-versed in M3’s configuration.
- Some interfaces still reflect legacy designs; requires training.
Resources
- Website: Infor M3
- Video: Infor M3 Overview
- Reviews: Capterra | G2
8. MKG 5
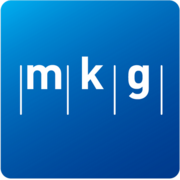
Overview
MKG 5 is an ERP system focusing on the metal and manufacturing industries in Europe. It offers planning, purchasing, sales, and shop-floor tools, tailored to small-to-medium outfits.
Key Strengths
- Industry Specialization: Targeted for metalworking and related fields.
- Clear UI: Screens and workflows designed to be straightforward for technicians.
- Local Support: Strong presence in the Dutch and German-speaking market.
Potential Considerations
- Primarily a regional solution, so global support may be limited.
- Fewer third-party integrations compared to more global ERP brands.
Resources
- Website: MKG 5
- Reviews: TrustRadius
9. Genius ERP
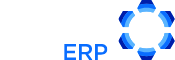
Genius ERP
Overview
Genius ERP is a complete manufacturing ERP system designed for small to mid-sized custom manufacturers. It supports make-to-order (MTO), engineer-to-order (ETO), custom-to-order (CTO), and assemble-to-order (ATO) production. Built by industry experts, it integrates CRM, inventory management, product engineering, job costing, scheduling, and accounting into one centralized platform. Though rooted primarily in North America, it also has a growing global presence.
Key Strengths
- Tailored for Custom Manufacturing
Streamlines complex workflows, from design to delivery, with robust BOM and engineering modules. - End-to-End Coverage
Consolidates critical functions—quoting, planning, tracking, and financials—into a single system. - Expert Implementation & Support
Offers onboarding and consulting to align the solution with specific business processes.
Resources
- Website: Genius ERP
- Video: Genius ERP Overview
- Reviews: Software Advice | G2 | SourceForge
10. MRPeasy
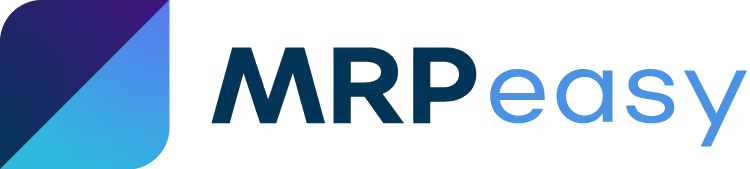
Overview
MRPeasy is a lightweight but capable cloud MRP/ERP option often adopted by smaller or scaling manufacturers. It emphasizes ease of setup, real-time inventory control, and simple production scheduling.
Key Strengths
- User-Friendliness: Short learning curve with minimal clutter.
- Ideal for SMEs: Affordable subscription options and straightforward functionality.
- Integrations: Connects easily with platforms like Xero, Shopify, and more.
Potential Considerations
- Focused on actual-cost environments; advanced cost reporting is limited.
- Might require workarounds for complex scrap or PPV tracking.
Resources
- Website: MRPeasy
- Video: MRPeasy Intro
- Reviews: Capterra | G2
(Always confirm each platform’s pricing, availability, and compatibility with your specific production workflows before committing.)
Conclusion: Pick an ERP-Software that Fits Your Needs and Budget
It can be difficult to figure out the best ERP system for your company. There are many different systems on the market, and it can be difficult to choose which one will work best for you.
You can’t achieve the maximum benefit of an ERP without a number of different systems working together.
This includes ERP, CAM, MES, CRM, and BI tools. Every software package has its strengths and weaknesses. As such, it is important to get an idea of what your business needs before deciding on your digital transformation journey.
Choosing the wrong ERP system for your company can have a huge impact on your production quality - from increase lead times, to lower accuracy in resource scheduling, to a lower level of customer satisfaction.
Don’t try to reinvent the wheel by yourself
I help companies around the world with independent advice in English, Dutch, and German. Get in touch today for your first free of charge call.