Ever thought about how to streamline your sheet metal manufacturing process? If you're using CNC machines, you'll need Computer Aided Machining (CAM) software for programming.
But here's the tricky part - picking the right CAD/CAM software solution for your needs can be like finding a needle in a haystack.
There are generic options, brand-specific ones, and even specialized solutions. So, how do you determine which one aligns perfectly with your specific machine and shop requirements?
It's not merely about making a choice; it's about making the right choice because this decision is intertwined with machine purchasing and system integration.
So, how do you currently tackle this intricate selection process?
Many successful fabricators start with an independent evaluation of CAD-CAM software systems. Today, I'm sharing a top 10 rundown at no cost to you
Below, you'll find the 10 most effective CAD-CAM software solutions for sheet metal and tube processing. These industry-renowned solutions have gained popularity through their usability and user experience.
These recommendations are not sponsored in any way and are 100% independent for you. The spotlight is on industry best practices here, so we're also diving into vendor-specific solutions.
I'm sure this will prove valuable to you and boost your operational efficiency both today and in the future.
The Top 10 CAD/CAM Software Packages for Sheet Metalworking
For this article, we've selected the following solutions. Click on the names to jump to the details, or directly explore some products and the vendor's website.
# | PRODUCT | DEVELOPER | HQ | AGNOSTIC |
---|---|---|---|---|
1 | TruTops Boost | TRUMPF | Germany | No |
2 | BySoft | Bystronic | Switzerland | No |
3 | CADMAN | LVD | Belgium | No |
4 | WiCAM | WiCAM | Germany | Yes |
5 | AlmaCAM | Alma | France | Yes |
6 | Libelulla | Libelulla | Italy | Yes |
7 | Lantek | Lantek | Spain | Yes |
8 | SigmaNest | SigmaTEK Systems | USA | Yes |
9 | Radan | Hexagon Software | United Kingdom | Yes |
10 | MetaCAM / Flux | TRUMPF MetaMation | India | Yes |
Disclaimer: Pricing, availability, and machine compatibility may vary based on your unique circumstances. This information is derived from our project experiences and selected online reviews. Always consult your vendor before making a purchase, as offerings may change. We accept no responsibility for your buying decisions or any disputes arising from this article.
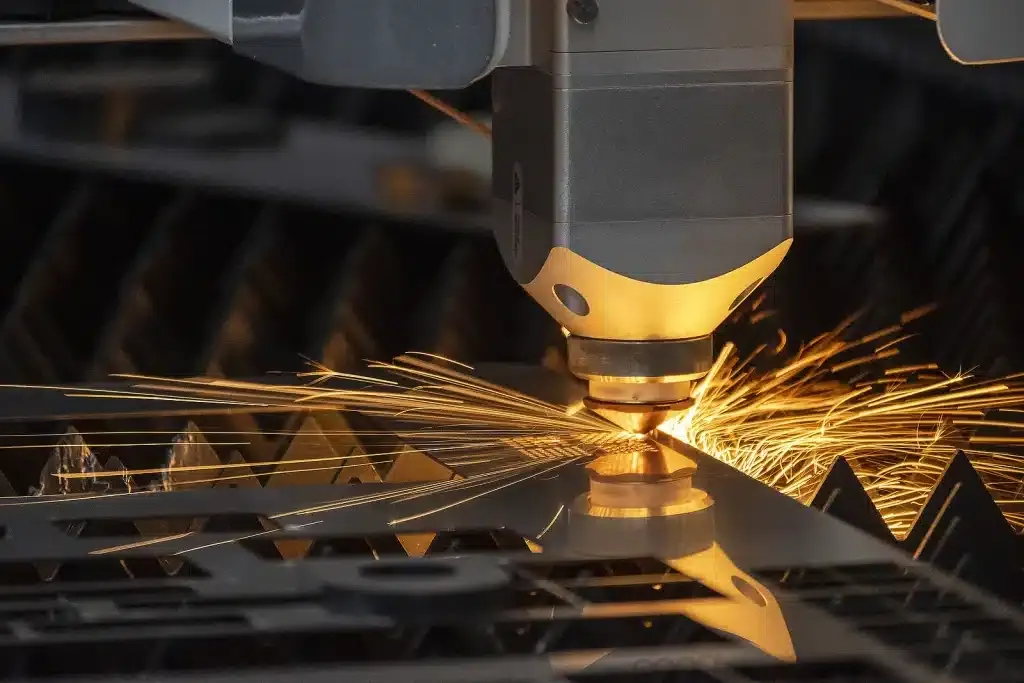
Introduction: Identifying the optimal CAD/CAM software for your fabrication workshop.
Picture this: You're gearing up to build a new shop or extend an existing one. Your first thought is probably about the machinery you'll need, right? Sheet metal fabrication machines are a hefty investment, no doubt about it.
But there's another key player who often gets overlooked: the software needed to run these machines. In today's world, your machine is practically useless without the right software—it either won't work at all or will only perform basic functions.
The tricky part? Many fabricators aren't even aware of all their options.
Some software providers only partner with certain brands, and some machine brands stick strictly to their own proprietary software. Then there's a whole gray area involving specific machine functions, converters, CAD conversion and—most crucially—integration options (but we'll get into that later).
So before you shell out for any new software—or worse yet, buy a machine without fully understanding its required software and how it fits into your overall ecosystem—make sure you've considered these points. Trust me; it'll save you from inefficiency and disappointment down the line.
Required for your smart factory
Ever thought about how to make your factory smarter? It all boils down to having the right features, fair pricing, and seamless integration. But with so many options out there, where do you start?
That's where I come in! I've put together a list of 10 potential software solutions that could be the perfect fit for your factory. Remember though, every factory is unique and might have specific needs.
Got any special cases or need them reviewed? Don't hesitate to reach out!
If you're feeling overwhelmed by over 30 vendors during a software procurement process, let me lend a hand. Together, we can whittle it down to your top three using clear buying criteria, and I'll provide unbiased advice on the big picture. How does that sound?
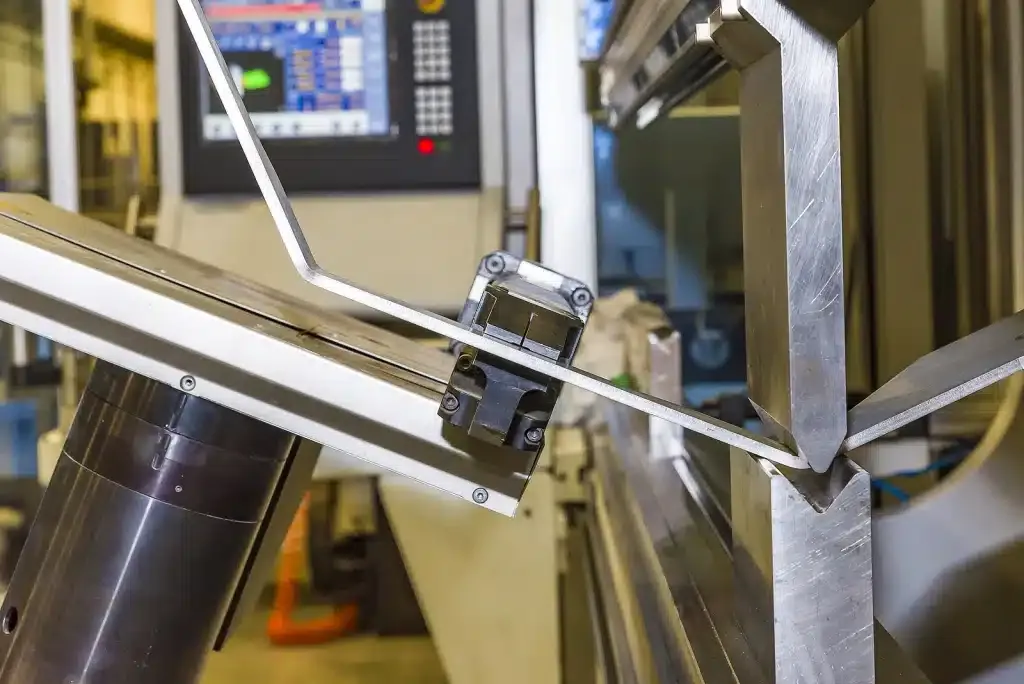
What is CAD/CAM Software?
Are you new to the world of sheet metal fabrication? If so, it's crucial to get a handle on CAD/CAM software. This stands for Computer-Aided Design and Computer-Aided Manufacturing software, which essentially bridges the gap between your digital designs and their physical realization in production.
Here's how it all comes together: With CAD software, designers can craft detailed 2D or 3D models of parts and assemblies. Then comes CAM software into play; it takes these designs, understands their geometries, and converts them into instructions fit for specific manufacturing processes like nesting or 3D simulations.
These instructions are then transformed into CNC (Computer Numeric Control) code that guides the machine tools. This code is responsible for every single movement of the machine - from precise cuts to bends - ensuring your metal sheets turn into exactly what you envisioned. And finally, these commands are executed by machines' PLCs (Programmable Logic Controllers).
TL;DR: CAD/CAM software is indispensable in sheet metal fabrication, transforming digital designs into precise machining instructions to optimize production. This integration significantly enhances efficiency, accuracy, and overall workflow in the manufacturing process.
Ever wondered if CAD/CAM equates to Industry 4.0?
Well, not exactly.
CAD/CAM is more of an Industry 3.0 marvel that played a key role in shifting from manual labor to automated machine operations. It marked a significant leap in manufacturing by enabling accurate control of machinery via digital designs. But just using CAD/CAM doesn't quite get you into the Industry 4.0 club.
To truly step into the realm of Industry 4.0, you need to blend CAD/CAM with other software and systems within your business framework - something that's not entirely commonplace today. You'll see what I mean when we dive deeper into system integrations with MES, ERP, and cloud applications in our upcoming discussion on integration.
Cutting, Bending, Rolling and more
The concept for all CNC-controlled machines is the same. For efficiency, most CAM software vendors offer a suite of options for each operation.
Solutions specifically designed for sheet metal fabrication, offline bending, and tube manufacturing have unique features. They should not be confused with similar CAM software for milling and turning.
The differences clearly lie in the end product, but also revolve around the fact that sheet metal is typically created from a single piece of raw material, known as a nesting.
Why CAD systems usually don't function as CAM in sheet metal.
Some CAD applications purport to offer CAM add-on solutions, but often lack the necessary depth and industry-specific expertise required for machine control.
Therefore, you should be cautious about treating this as a minor task. A feasible solution will focus on your machines and their specific technologies.
The challenge is that you need nesting for both cut sheets and tubes. To unfold sheet metal parts accurately, it's advisable to use machine-specific data like V-die, which requires offline programming. Certainly, you can unfold CAD-files using a solution like Inventor, SolidWorks, or even Fusion add-ons for conversion. However, preparing the actual machine-ready solutions demands more.
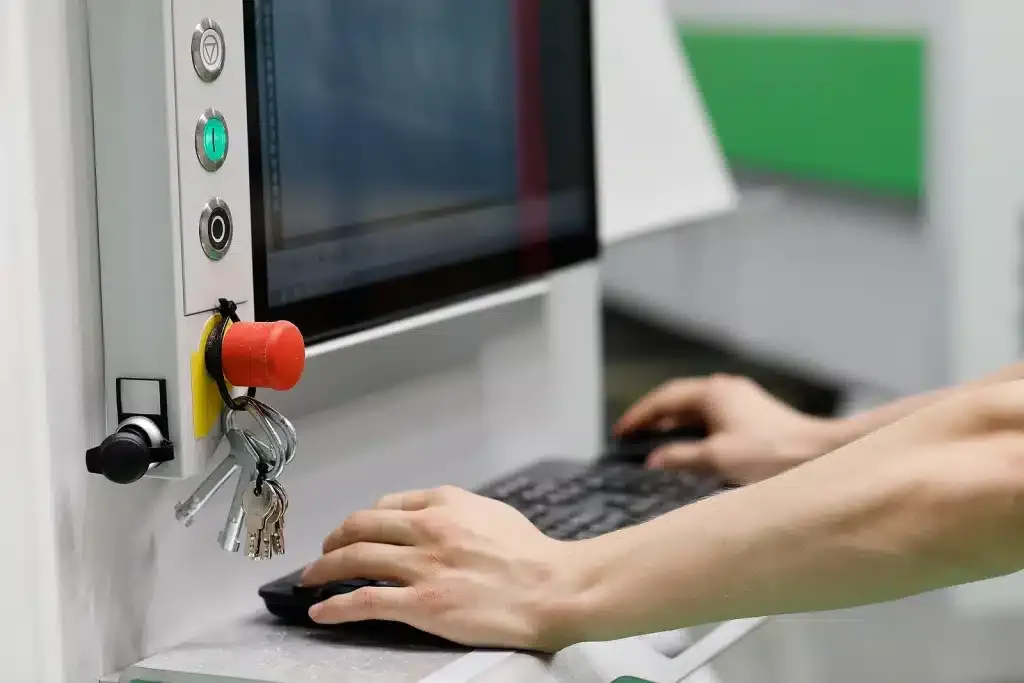
Three main operations in custom fabrication
In this discussion, we're zoning in on three key operations:
- 2D Sheet Cutting and Punching
- 3D Tube Processing
- 3D Sheet Metal Bending
You might be thinking, "Wait a minute, we do more than just fabricate!" And you're absolutely right. Tasks like welding, assembling, tube bending, post-processing and surface treatments are all part of the job.
Now you might be wondering why tube processing made the list.
It's a bit of an outlier since it's like working with a thin sheet that decided to go round instead of flat. But here's the thing - our goal is to find an integrated solution for your entire operation. That’s why we’re not leaving any stone unturned.
Sure there are plenty of laser cutting, bending and tube software programs out there. Consider this as your launch pad into that world.
The last thing you want is juggling multiple software systems for each machine brand or technology - it’s costly and maintenance-heavy! So let's broaden our horizons together to find the perfect solution partner for you.
CAD/CAM for Sheet Cutting
This technology involves creating nesting plans, also known as sheet layouts. These plans incorporate the machine's technology, which often determines the speed of the tool paths and piercings, along with various optimizations such as collision avoidance.
A proficient sheet cutting software will accommodate all the technologies in your machine, enabling optimal operational output. The most crucial element is a table detailing machine parameters to gauge laser power (similarly for plasma) and machine feed speeds, among other things.
Furthermore, contemporary machines come equipped with logistical solutions like loading and unloading techniques, and even fully automated Flexible Manufacturing Systems (FMS). More frequently, a CAM solution also provides necessary instructions for proper loading and unloading.
CAD/CAM for Tube Cutting
Tube cutting software operates similarly to sheet cutting, generating CNC codes to control machine movements and the power directed to the cutting head, aligning it with the production design requirements.
Many vendors who develop sheet-cutting software also include tube-cutting functionalities or offer them as add-ons due to the similarities between the two systems, catering to metalworking companies that utilize both technologies.
Tubes are nested based on the X axis, which represents the length of the base material, making the nesting process simpler.
However, most machines offer 3D cutting, where the cutting head moves along the X, Y, and Z axes, often referred to as a bevel cut. This requires more complex programming to execute correctly.
CAD/CAM for Offline Bending
Offline bending doesn't require you to program your bending cell directly onto the machine, hence the term 'offline'.
Instead, the programming is done at a separate workstation, concurrently with production. This eliminates the need for time-consuming machine training, thereby increasing machine availability and allowing for continuous operation.
Interestingly, this has nothing to do with your internet not working. In fact, your machine will typically need to be connected to the network to do this effectively. I would say that running around with a USB drive is not particularly efficient.
To create an effective program for a bending machine, remember that bend deductions, which change when the machine's tooling is adjusted, must be considered. This is why programmers frequently use 3D-CAD models to develop their programs, as it allows them to update the design multiple times to meet production requirements.
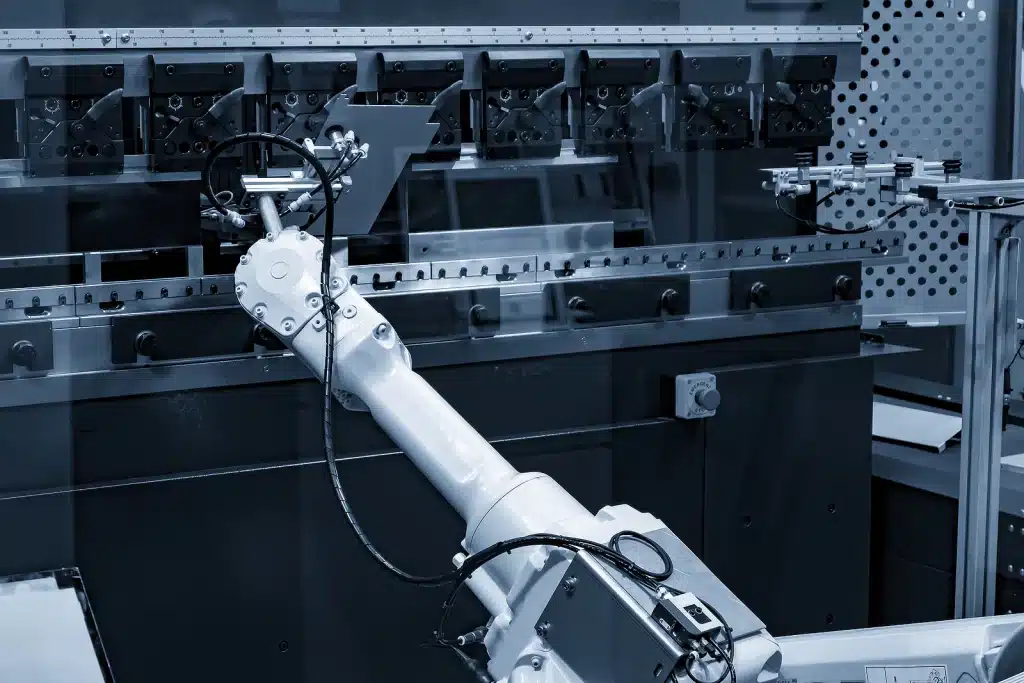
Buyer's Guide: Choosing the Right CAD-CAM Software
Choosing the perfect CAD-CAM software for your business involves several important considerations to ensure compatibility, efficiency, and user-friendliness:
- Machine Compatibility: Ensure the software is compatible with your existing machinery, and in the case of post-processors, confirm there is no data loss.
- Integration Capabilities: Search for software that can seamlessly integrate with other systems in your production line, such as ERP, MES, or quality management systems.
- Support for CAD File Formats: The software should support all relevant CAD file formats used in your industry to ensure smooth workflow transitions.
- Customizability: Opt for software that permits customization to accommodate the specific needs and unique workflows of your operations.
- Local Support and Training: Choose providers who provide extensive local support and training to help your team use the software effectively.
- User Interface Design: A user-friendly interface is vital for efficient operation and reducing the learning curve for new users.
- Maturity Level of the Software: Consider the software’s track record and maturity in the market, which often indicates reliability and robustness.
- Software Specificity: Decide whether a generic (brand-agnostic) or machine-specific solution best suits your needs. While many machine vendors offer proprietary software, brand-agnostic solutions may provide more flexibility and potentially broader functionality.
Optimal CAD-CAM software not only maximizes your machines' potential but also enhances productivity through a user-friendly interface and robust support. Make an informed decision to fully benefit from this technology.
CAD-CAM in cloud?
At this stage, some vendors have begun transitioning their offerings to the cloud. This means installations, such as those in the web browser, are no longer required. For instance, TRUMPF's Startup ScaleNC even offers to program the machine for you.
There are some precautions to consider:
- Data transfer to the machines
- Security and stability
- Cost of ownership
I believe that CAD-CAM in the cloud is the future, but current industrial requirements make this challenging. However, I anticipate that ERP and CAD will transition fully to the cloud in the near future.
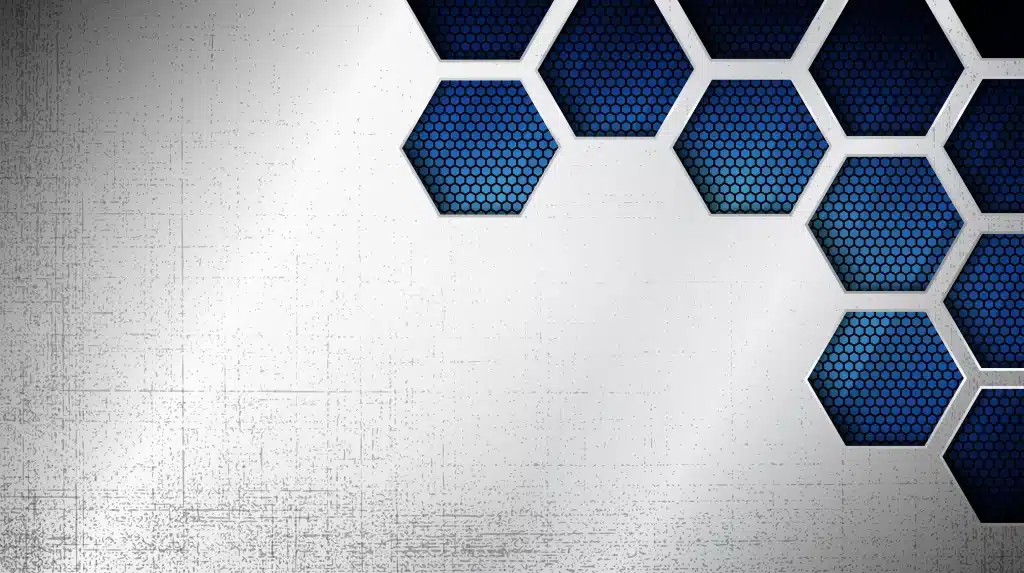
10 Top CAD/CAM Suites for Sheet Metal Processing, Bending, and Tube Handling
Below, I've listed 10 vendors along with their products.
Please note: The order does not imply any ranking; it's simply a source of inspiration. Your situation may greatly differ from that of your colleagues, depending on your industry maturity, budget, machinery, and experiences.If in doubt, consult your vendor or seek professional advice during your selection process. Additionally, all brands belong to their respective owners.
# | Product | Developer | Sheet Cutting | Tube Cutting | Bending | HQ | Agnostic |
---|---|---|---|---|---|---|---|
1 | TruTops Boost | TRUMPF | Trutops Boost | Programming Tube | TecZone Bend | Germany | No |
2 | BySoft | Bystronic | BySoft CAM | BySoft CAM | BySoft CAM | Switzerland | No |
3 | CADMAN | LVD | CADMAN L | No | CADMAN B | Belgium | No |
4 | WiCAM | WiCAM | PN 4000 | No | PN Bend | Germany | Yes |
5 | AlmaCAM | Alma | AlmaCAM Cut | AlmaCAM Tube | AlmaCAM Bend | France | Yes |
6 | Libelulla | Libelulla | Libebulla.CUT | Libellula.TUBE | Libellula.BEND | Italy | Yes |
7 | Lantek | Lantek | Expert Cut | Flex3D | Flex3D | Spain | Yes |
8 | SigmaNest | SigmaTEK Systems | SigmaNEST | SigmaTUBE SW | SigmaBEND AP | USA | Yes |
9 | Radan | Hexagon Software | RadNest | RadTube | RadBend | United Kingdom | Yes |
10 | MetaCAM / Flux | TRUMPF MetaMation | CUT CAM | 3D Cam | Flux Bend | India | Yes |
1. TRUMPF TruTops Boost
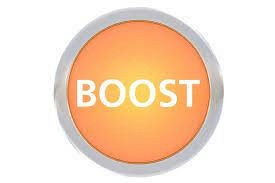
TRUMPF TruTops Boost, developed by TRUMPF Co & KG from Germany, is a leading industry solution. Despite its brand-specific nature, it illustrates the harmonization of an excellent user interface, deep CAD integration, and machining.
The software is particularly suitable for fabrication shops that perform laser cutting, punching, and bending. Tube cutting is enabled through additional modules that interface with their Oseon software suite, which also encompasses MES/PPS and even basic ERP functions.
In the software suite, some modules include CAD (SpaceClaim engine) and CAM post processors for all TRUMPF Machines.
The software comes with features such as batch editing, automatic imports, and API integrations, and is available almost globally.
Product links
[ Software link ] - [ Demo Video ]
2. Bystronic BySoft CAM

BySoft, developed by Bystronic AG based in Switzerland, is designed for companies using their machines. It simplifies the efficient and intuitive creation of cutting plans for laser cutting machines, as well as plans for bending and tube lasers.
The software offers a comprehensive suite of modules that assist with various steps in the process, including CAD and nesting. The Plant Manager module manages order pools. Modules like CAD Importer, SolidWorks Add-in, and Offline Programming are also available in the suite.
Most common CAD files are supported, and links to ERP and PPS/MRP are common. The software vendor is also considered globally available.
Product links
[ Software link ] - [ Demo Video ]
3. LVD CADMAN

CADMAN is a suite of products by LVD, a Belgium-based company with an international presence. This software is designed to operate with LVD machines. The suite includes modules with functions such as Smart Drawing Importer (SDI) for various CAD file formats, and other modules for cutting, bending, punching, automation, and handhelds.
Therefore, CADMAN serves sheet metal cutting and bending. Currently, it does not support tube operations (as of writing).
The software is praised for its accuracy, simple import interface, and flexibility in terms of integration and customisation. Availability is considered global.
Product links
[ Software link ] - [ Demo Video ]
4. WiCAM
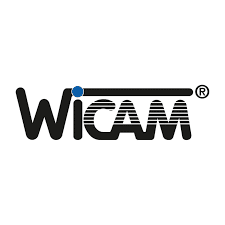
WiCAM, a brand from Germany, offers various products for sheet metal fabricators. They are particularly known for being truly agnostic, capable of integrating with almost all known brands through their own postprocessors. WiCAM is also considered more budget-friendly compared to larger competitors.
In the software suite, some of the modules include PN4000 for cutting, PNControl for order management, PNCalculate for quoting, and PNBend for offline programming. The software features ERP, PPS, and MES integrations. It's also considered to be globally available, with a strong presence in Europe.
Product links
[ Software link ] - [ Demo Video ]
5. AlmaCAM
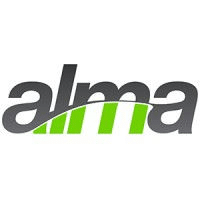
AlmaCAM, developed by the French company Alma, is a software suite with a strong emphasis on nesting solutions. It integrates various CAD/CAM software applications for tasks like cutting, punching, bending, welding robot programming, etc., within a secure data management system. Additionally, it offers modules for quotation calculation, production control, and integration with other information systems
The software is agnostic, meaning it can function with a wide variety of machine brands and integrate with numerous third-party systems, including ERP, PPS, and Quoting. Its distinguishing feature is its expanded offering into areas like CAD imports, including support for assemblies, 3D CAM (tube cutting), and robotic welding.
The software is also available in most countries worldwide, either through their own offices or a reseller network. It's also worth mentioning their efforts to launch web-based nesting tools, such as Nest & Cut and it’s connected WebQuote solution.
Product links
[ Software link ] - [ Demo Video ]
6. Libellula
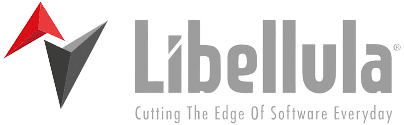
The Libellula suite, developed by Italy-based Libellula S.R.L., is renowned for its wide range of applications. These include 2D cutting, 3D offline bending, job shop management, warehouse management, and ERP integration. The company is considered agnostic, primarily partnering with smaller, more cost-effective brands in Europe.
Their most utilized solution is CUT, a software that can program all types of cutting machines: laser, plasma, oxycutting, and water jet. This software is designed to optimize cutting results by conserving material, reducing time, and simplifying the operator's task through a high degree of automation.
It's also worth mentioning that they offer solutions for tube cutting, HVAC design, 3D machine design, and so forth, including their new workflow solution, Fable.
Through their extensive network, they offer global services, primarily focusing on Europe, with offices in the Middle East and China.
Product links
[ Software link ] - [ Demo Video ]
7. Lantek Expert / Flex 3D

Lantek, based in Spain, offers a comprehensive suite of software solutions for sheet metalworking.
Their most renowned product, Lantek Expert, is an advanced CAD/CAM nesting software system designed to automate the CNC programming of sheet metal machines. It provides nesting algorithms and mechanization strategies for all types of cutting (laser, plasma, oxy-fuel, water jet technologies) and punching machines.
Their suite is also enhanced by Lantek Flex3D, a 3D CAD/CAM software that automates the CNC programming for 3D machining of tubes, pipes, beams, profiles, and sheet metal. The software is integratable with their own native MES solution, Quoting & ERP integration, and various apps for analytics and integration purposes.
The software is agnostic and has existing relationships with the largest makers, making it interesting if your shop has various brands and integration needs.The software is available globally through an extended reseller network.
Product links
[ Software link ] - [ Demo Video ]
8. SigmaNest
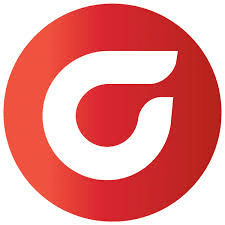
SigmaNEST CAD/CAM, a software suite developed by SigmaTEK Systems in the United States, operates most fabrication machines from a single platform that scales to your needs. This includes Tube Nesting, Beam Line Nesting, Press Brake, Unfolding, and DSTV File Conversion.
The software programs a wide range of machines such as laser, waterjet, plasma, and more. It allows programming for various materials like steel, wood, and composite materials. Parts can be imported from any major CAD system and sorted by material and machine for efficient use of materials and machine operation.
Businesses of all sizes find value in SigmaNEST's comprehensive features, which include work order management, quotes/estimates, inventory control & tracking, NC simulation, and data integration. It is available globally through their US headquarters and various offices.
Product links
[ Software link ] - [ Demo Video ]
9. RADAN
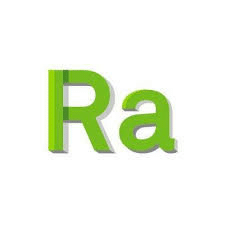
RADAN, created by Hexagon, is particularly suitable for the metalworking industry. This machine-independent software can operate with various types of machines, including laser, plasma, water jet, and flame-cutting machines, without needing specific adaptations for each one.
The software suite includes modules for punching, profiling, bending, nesting, and drafting. It also features Radquote for quick quoting, Radimport for easy data importing, and Radbend for offline press brake programming with 3D simulation.
The software offers advanced features such as true-shape nesting, design tools, multi-axis programming, and an estimate-to-invoice process. This toolkit enhances productivity and reduces lead times in sheet metal fabrication. It is globally available.
Product links
[ Software link ] - [ Demo Video ]
10. TRUMPF MetaCAM / Flux
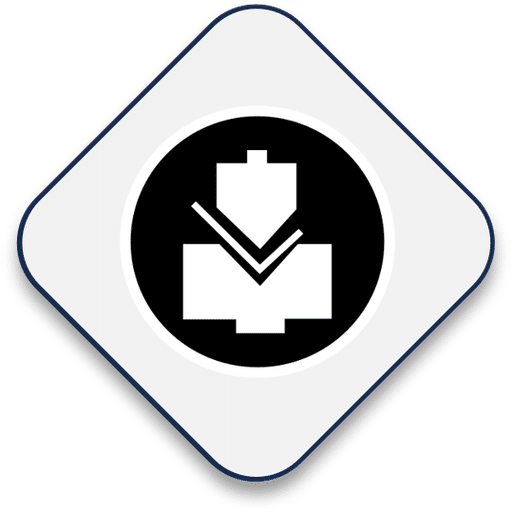
Flux, developed by TRUMPF Metamation/Flux, is a versatile product suite tailored for the sheet metal sector.
It is renowned for its TecZone 3D engine, known for its precision in sheet metal processing, which has seamlessly integrated into TruTops Boost for offline bending. Flux offers nesting and processing solutions for laser and punch operations, along with bending software named MetaCAM.
The software suite caters to various needs in sheet metal fabrication, including material optimization, tool arrangements, CAD import and design, planning and simulation, and cutting optimization.
With its agnostic approach, Flux seamlessly integrates with diverse hardware and software platforms commonly used in the industry. Available globally, Flux empowers manufacturers worldwide to streamline their operations and enhance productivity.
Product links
[ Software link ] - [ Demo Video]
Other notable solutions in the industry
There are a few CAD-CAM systems that, while noteworthy, didn't quite make our list. These include specialized software from Salvignini, Prima Power, Metallix, Messer Omni Win and various Asian options not yet globally accessible.
Don't get me wrong - this doesn't mean these solutions are subpar or won't fit your business needs. It's just that they were either too niche for our criteria or not available worldwide. Some were tied too closely to a specific machine brand or we simply couldn’t review them based on our exact requirements.
Are you a vendor who believes your software deserves a spot here? Feel free to reach out! I'm more than happy to consider your product and potentially update or add its description.
Looking for more resources?
The Fabricator, an esteemed blog in the metals industry, offers an extensive CAD-CAM software buyer's guide which might be handy in your search. It has a strong focus on U.S.-based brands making it especially useful if you're operating in that region.
https://www.thefabricator.com/guide/cad-cam-software
What do you think about these additional resources? Have any piqued your interest? Please let me know via a LinkedIn message or an email.
Seeking advice tailored to your unique needs?
You're in the right place! We've got a treasure trove of over 50 sheet metal fabrication software systems, each tailored to different industry needs.
This post is just a sneak peek; imagine what you could uncover with our comprehensive consulting services. Regardless of your location, we're here to guide you remotely.
So why wait? Reserve your spot today and let's start exploring together!
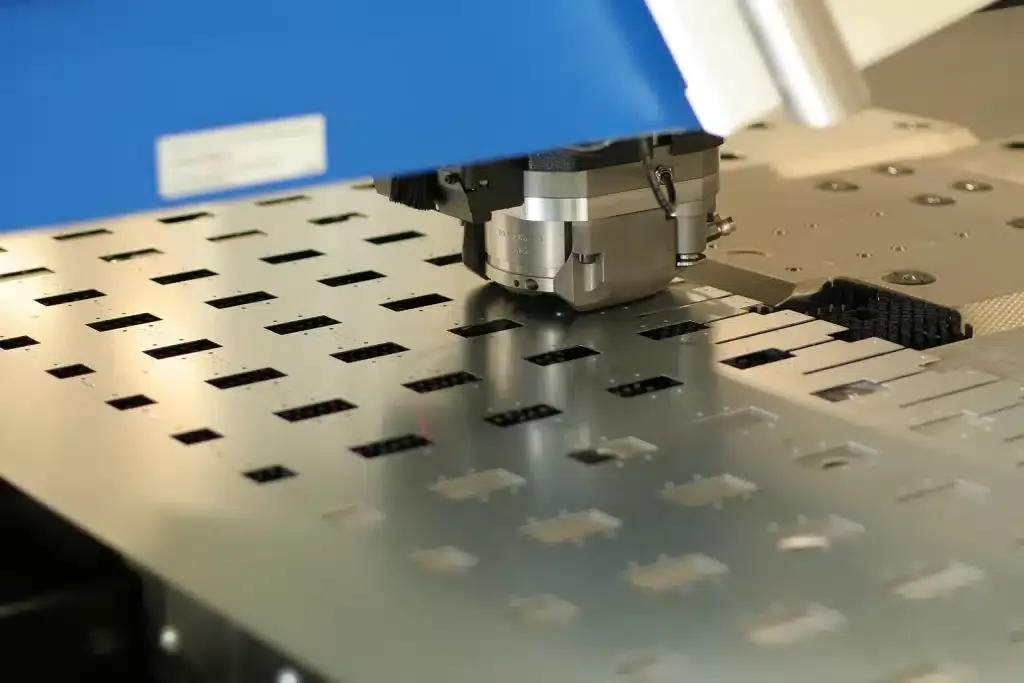
Navigating the Selection and Implementation of CAD-CAM Software in Sheet Metal Fabrication
Selecting and integrating CAD-CAM software into your sheet metal fabrication process is no small task. It's about balancing your immediate requirements with future expansion plans. So, how do you make the right choice? Let's dive into some practical guidelines to help you on this journey:
Machine Brands and Post Processors
Ensure that the CAD-CAM software you select can generate accurate post-processor code compatible with your CNC machines. This compatibility is vital for ensuring the software can communicate effectively with the machines you use, which impacts both the quality and efficiency of production.
Budget Focus vs. Long-Term Investment
While initial costs are a significant factor, consider the long-term benefits of investing in quality software. Cheaper or brand-agnostic options might offer short-term savings but could lead to higher costs in the future, especially when scaling up or requiring specific customizations or integrations.
Local Support and Training
Opt for a software vendor that offers robust local support and training options. This ensures that your team can maximize the software’s potential and address any issues promptly, reducing downtime and maintaining productivity.
Team Technical Know-How
Evaluate the technical capabilities of your team and ensure the software’s complexity matches your team’s skills. This alignment is crucial for smooth operation and fully leveraging the software’s features without overwhelming your staff.
Flexibility for Future Changes
Remember, your chosen solution isn’t permanent. With a strategic setup that includes the right core data—such as material types, part articles, machine specifications, and coding—you can more easily switch to a different system in the future if needed.
Integration with ERP and MES
From the outset, consider how the CAD-CAM software will integrate with your Enterprise Resource Planning (ERP) and Manufacturing Execution Systems (MES). Successful integration minimizes the need for manual data entry, streamlines workflows, and improves data accuracy across your operations.
Additional Considerations:
- Team Training Needs: Assess and plan for ongoing training to ensure your team remains proficient with the software and new features.
- Budget Planning: Factor in both the purchase price and the cost of integrations, training, and potential expansions.
- Future Machine Purchases: Consider whether the software will remain compatible with any new machines or technologies you plan to introduce.
- Customization and Flexibility: Look for software that offers customization options to tailor workflows and processes to your specific needs.
- Accuracy and Reliability: Prioritize software known for its accuracy in design and reliability in performance, which are critical for maintaining quality standards.
- Software Updates and Longevity: Choose a provider that regularly updates their software to keep up with industry changes and technological advancements, ensuring your operations stay current and competitive
These points will guide you in selecting a CAD-CAM system that meets your current requirements, supports your future business growth, and adapts to changes in the manufacturing landscape.