Have you ever tried to process modern CAD-files automatically, making your factory paperless?
If so, you'll know that it's difficult because you probably receive .DXF and .STEP Files from your customer, but also technical drawings in .PDF format.
To process a customer request, you'll still have to manually enter those files into your system, perhaps print the instructions, and get everything organized.
What do you do if you want to automate your work intake? Some manufacturers have found success by using Model-Based Definition (MBD) and moving away from printed work instructions to interactive 3D-models with manufacturing information.
But there are a few things you should know before you start with this right now, to prevent your costs from spiraling out of control.
It is important to keep up with the latest technologies, but not all solutions are ready for the highly specialized metal fabrication market. You can't just buy an MBD-viewer and then get started; you'll need to think the process through from work intake to finish production.
So what is the right strategy?
This article will tell you what you need to know before you get started with MBD. We'll look into common best practices, suitable file formats like QIF, JT, and IGES, what the current state of the market is, and which solutions you can start with today.
Curious how this fits into your digital factory strategy? Take a look at my consulting offering:
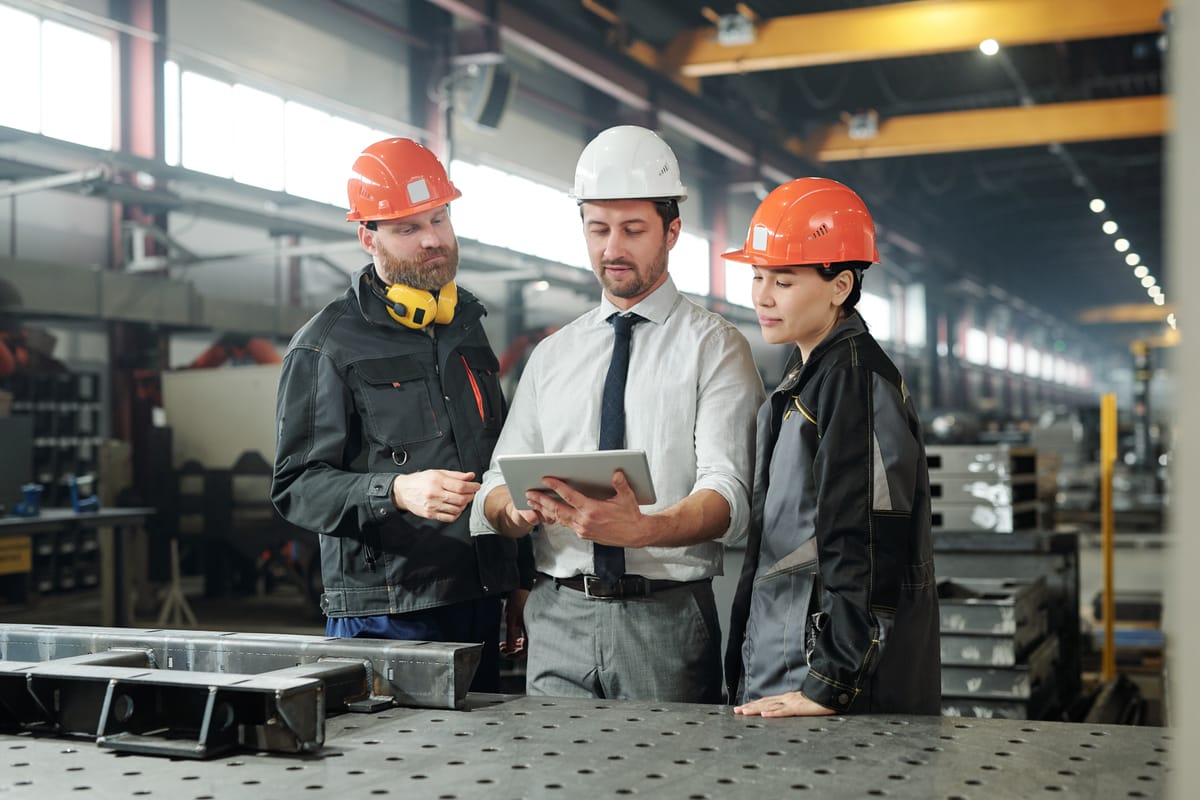
What is Model Based Definition (MBD)?
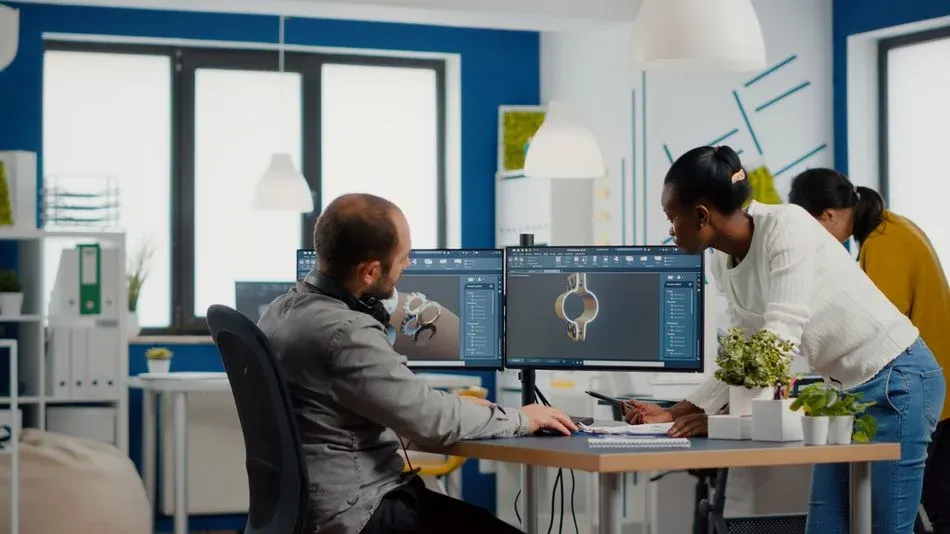
Model-Based Definition (MBD) is a technique to include manufacturing and design information in a 3D-model instead of using traditional 2D-technical drawings.
It's the process of using annotated 3D CAD models that include semantic PMI (manufacturing data) to be the definitive authority throughout the product lifecycle.
It's already commonly used in high-tech sectors such as aerospace and military applications and is continuing down the supply chain. As you guessed, it's also used in the metal fabrication market.
Why is this such a big thing?
The main goal of this guarantee is to ensure the quality of the assembled product by having both instructions and a place to check for tolerances and quality without leaving the model.
The new 3D CAD model-based workflow will allow designers to connect more easily with one another because of a central source of truth for design, preparation, manufacturing, and quality control.
The term "model" refers to any representation of a single part that can be used for reference or verification purposes. Models are created using CAD software such as Revit, AutoCAD, CATIA, and Solidworks. These models can be edited and used for various purposes in the fabrication process.
By capturing and conveying manufacturing requirements in a 3D-model instead of 2D drawings, a model becomes machine-readable and makes it easier to automatically process the drawings and get to production faster with higher accuracy.
The most important takeaway of MBD is the interoperability of data so that a fully digital factory can be achieved. It is crucial for Industry 4.0 or Model-Based Enterprise in which the data can flow seamlessly through the enterprise and even be exchanged with suppliers in a unified way.
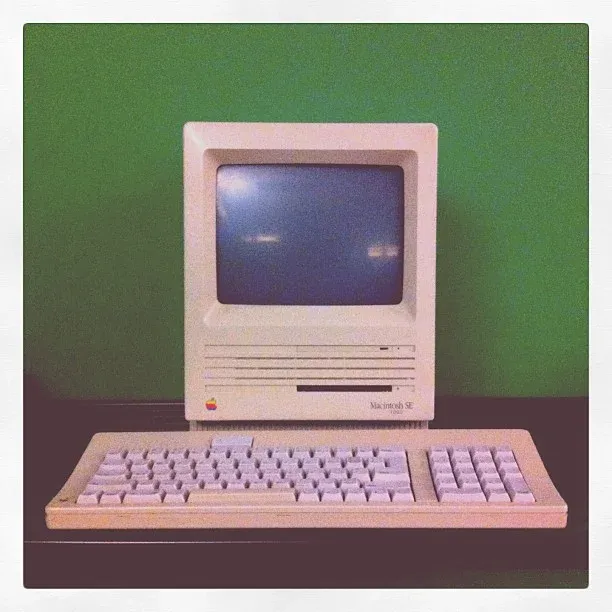
The history of CAD-files and MBD
CAD files as we know them have been around since the 1980's. They were developed to improve machining accuracy and performance by allowing engineers to change the parameters of an existing design or create a new one from scratch.
These files were primarily used for modeling purposes, but over time, CAD-files became an integral part of metal fabrication as well.
The CAD files we use today were designed to be used in any context where a computer could interact with a model. However, in the past 20 years, CAD-files have become more and more complex.
Without going into detail about each file type, the following is a brief history of how CAD-files came about and what their role is today.
The 1960鈥檚 - First CAD systems
The first mentions of CAD files are from the 60s. This was when the invention of the computer led to the DAC (Design Automated by Computer), CADAM (Computer-Graphics Augmented Design and Manufacturing) and Computervision. This is where is all started.
The technology was only used by military and universities at this stage.
The 1980's - 3D CAD - The Beginning
AutoCAD was launched in 1982. This started the launch of commercial applications for manufacturing companies.
Back then computers supported the drawing process, but the output was always a 2D printed document.
Matter fact, you needed special and costly printers (they were called plotters back then) to get the desired output. There was no exchange between PC鈥檚
The 1990's - 3D CAD/CAM Moves to the PC
First, the 3D wireframe models were only used to create the 2D print of it. It wasn鈥檛 until many years later that the CNC technology was introduced, which contained 3D coordinates for the machine to operate.
Solid modeling started to appear in PC software around the mid-1990s. That was when it was possible for the first time to share solid models in IGES, STEP, ACIS, and Parasolid formats.
This also came with the invention of the Portable Document Format (.PDF) to no longer have to print 2D technical drawings, but to send them over digital channels.
The now commonly used file format .STEP was also invented around 1995, which we'll dive into further in the article.
The early 2000鈥檚 - The internet and interexchange of files
Manufacturing businesses started to slowly connect to the internet before that, requirements were exchanged through fax or shipped per mail (most common).
Now, the internet has made it possible to exchange CAD files over email. There was a huge boom of new software systems, the ones we work with today.
The early 2010鈥檚 - Modern CAD-file formats
The market has become more and more competitive and demands for quality and speed have increased significantly.
Since the early 2010s, larger CAD-makers have started working on their own implementations of file formats that include more information, which we call Product Manufacturing Information (PMI).
National organizations such as the National Institute of Standards and Technology (NIST) in the United States are working daily to standardize the field and as a result, new universal formats that are no longer tied to a specific CAD vendor are being developed.
CAD and Engineering Documentation Today
A PDF and 3D model (commonly in .STEP) is the standard deliverable now used by most small companies and requested by the suppliers. We call this complete package of information TPD: Technical Product Documentation, which engineers are required to deliver to a manufacturer to guarantee production quality.
It takes nothing more than a compatible CAD/CAM system that can import the native or neutral 3D CAD model and an Adobe reader to access the information. The STEP-file format has now been widely accepted and has made significant expansions in terms of data that can be included in the file.
This leads us to the start of Model Based Definition and STEP AP242 of today.
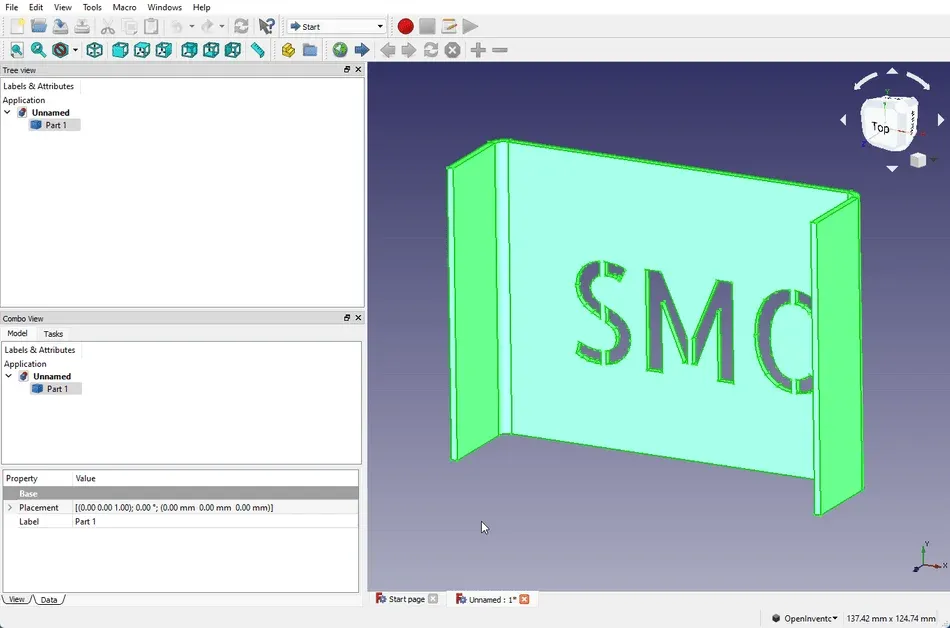
STEP-files
What is a STEP-file?
STEP stands for Standard for the Exchange of Product Data (STEP).
It's a neutral file format that's not dependent on the CAD software you're working with. It contains information about 3D objects and is typically used to transfer 3D data between different CAD and CAM programs. It's the most popular file format globally for exchanging 3D models.
There are many CAD software tools that support STEP files, including AutoCAD, Fusion, SolidWorks, OnShape, PTC Creo, CATIA, and ArchiCAD.
These programs can export to this file, and there are free viewers and converters available so that manufacturers can use this format without extra cost.
The most commonly used and versatile is Autodesk Fusion 360 since it runs on Windows, macOS, and mobile devices, as well as through a web browser.
Alternatively, you could try FreeCAD, ABViewer, TurboCAD, CATIA from Dassault Systemes, and IDA-STEP. There are also free online STEP/STP viewers from eMachineShop and ShareCAD.org.
You can find the best examples below:
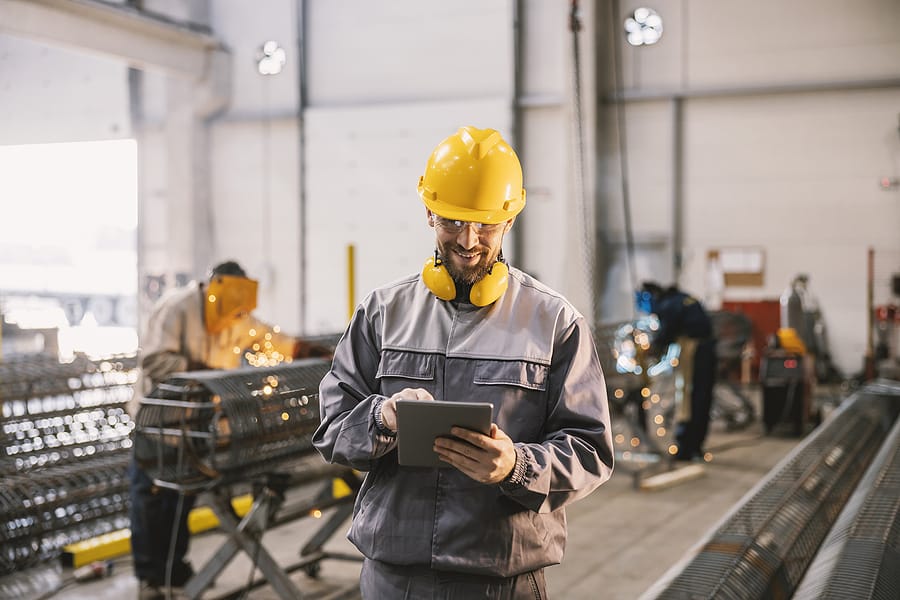
A highly accurate standard for manufacturing:
A STEP-file is a mathematical representation of a curve, stored in a NURBS specification. The NURBS specification is capable of storing data with exact precision.
This level of precision cannot be achieved using the polygon and triangle representations utilized by visualization-oriented alternative file formats that are used in more creative sectors.
NURBS representations are used by CAD files because they allow for the final manufactured creations to have perfectly smooth curves, like nicely rounded iPhone cases or beautiful sweeps on car bodies.
The STEP file format is focused on the transfer of shape and form, not on visual appearance for such a lack of textures and lighting. It's made for manufacturing, not for high-fidelity graphical purposes such as video games.
The history of STEP-file standards (AP203, AP214, AP242)
The first inception of STEP was with AP 201, where basic designing was possible. This has been expanding over the course of the years. AP 203 kicked off Configuration Controlled Design. This format contains information such as geometry, topology, but also some product information (names of parts).
STEP AP 214 was then released, which transfers extended product data, including assemblies (organizational data, assembly structure, parts list data, edge, surface, and volume models, color, line width, shaded display, drawings, material information, surface properties, tolerances).
STEP AP 214 is the standard for the automotive industry and is therefore also widely used in metal fabrication. Most commonly, CAD-software will export in AP 214 by default.
The latest development is STEP AP 242: where it merges STEP AP 203 and AP 214 to create a single standard for model-based 3D engineering.
In addition to the functionality familiar from AP 214 or AP 203, the following functionalities have been added in AP 242: Shape data quality, 3D-Tesselated geometry, 3D Product Manufacturing Information (PMI) with semantic representation, Access right management.
What this means is that a model can contain the manufacturing instructions within the 3D-file, which in theory eliminates the need for a 2D-drawing. This claim has been argued against at this stage, though, which we鈥檒l come back to later in the article.
Other formats
QIF
QIF is a newer ISO-standard format with the most robust scope on MBD, especially semantic PMI for human- and machine-readable CAD downstream for automation, analytics, and Big Data.
As the name suggests, it's specifically created for quality control and measurements of such. It's not designed for the same goals as a STEP file.
Nevertheless, it's a very modern take on MBD with advanced concepts like tolerancing and measurement features, support for assembly-level PMI, and more.
The format has gained traction in the metrology and quality departments but is not commonly used in the manufacturing of metal parts. If it is being used, it is added to other manufacturing such as STEP-files.
JT Open
JT is known for its visual representation, but it can also include B-rep and PMI, making it also MBD-ready. However, it is not used by many manufacturers, who require converters if they want to use the format.
Although technically an open format, many vendors use Siemens' JT Open Toolkit, which makes use of proprietary recipes, so it's less common outside Siemens software environments.
Why use MBD?
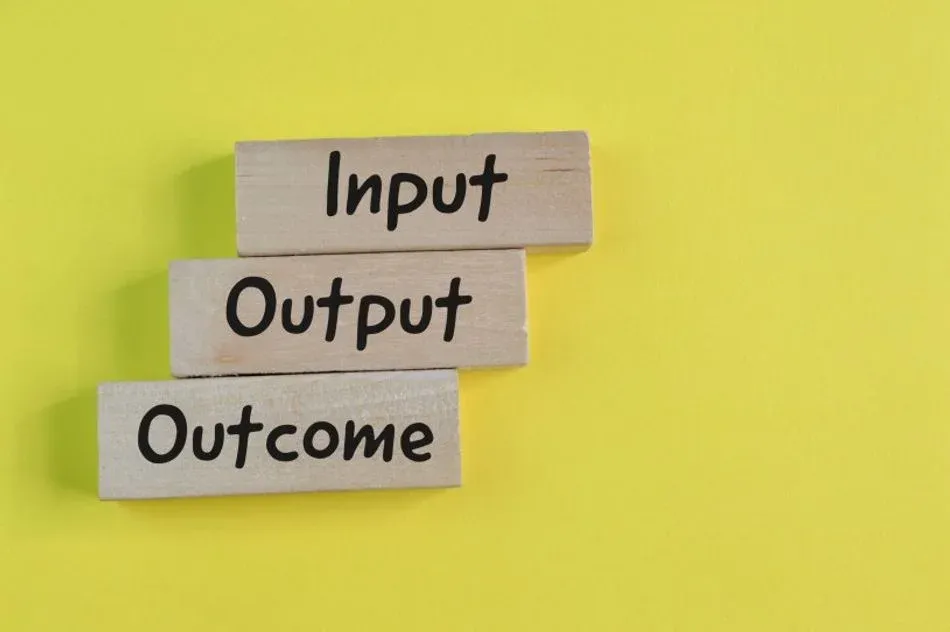
If you're a manufacturer, for example, if you fabricate metal parts, your business nowadays will typically be working with a variety of 2D and 3D drawings. For example, in the .DXF and .DWG formats for 2D and .STEP for 3D models.
Going from a drawing to a quote and then to production requires you to read the drawing and then enter the requirements in your software. This can be a time-consuming activity that is sensitive to errors.
MBD seeks to automate this process so that the information in the drawing is stored in a 3D model that is machine-readable. It also attempts to reduce the steps necessary and prevents silo's from existing in processes.
By doing so, we can increase the speed of our work processes, improve accuracy, and be more efficient in producing complex products.
With Model Based Definition (MBD), all product and production-related information is stored in one digital model. In addition to the 3D solid model of the design, additional characteristics such as description, material type, dimensions and tolerances, etc. are also stored in one data carrier. This is called Product Manufacturing Information (PMI).
PMI is used to digitally exchange data between systems (semantic data) or to visualize data, for example for paperless production control.
The benefits of Model Based Definition:
There are lots of potential benefits to MBD if it鈥檚 implemented well:
- Production processes can be streamlined accurately by minimizing costly and time consuming 2D drawings
- Chances of errors are reduced due to 3D interactive models with rich meta properties
- It becomes easier to comply with industry standards
- Time required to re-model parts based on 2D drawings is eliminated completely
1. Capturing and using data early in the process
A significant principle in digitization is to record information as early as possible in the process in a universally standardized manner.
This has two major advantages:
- The information can be reused more often. This saves time and prevents possible input errors. Because more information is available, an employee or a system can make more informed choices. Think of the choice of how a product should be made. More extensive information is often also necessary to further automate processes.
- An additional advantage is that there is a better basis for looking for connections when analyzing the product and production data (big data). Model Based Definition (MBD) offers a good starting point for capturing all relevant data in a universal way.
2. Time savings for higher-level work
Because the modeling is done more automatically and reading of the files automated, an engineer could in theory spend more time on higher level work instead of having to make 2D-drawings, print those, and spend time organizing PDFs.
3. Being on the same page (digitally)
One model that is used from design to production and quality control, creating short feedback loops. This means that there is one file that can be relied upon over the course of the entire process.
Must we all get started with MBD?
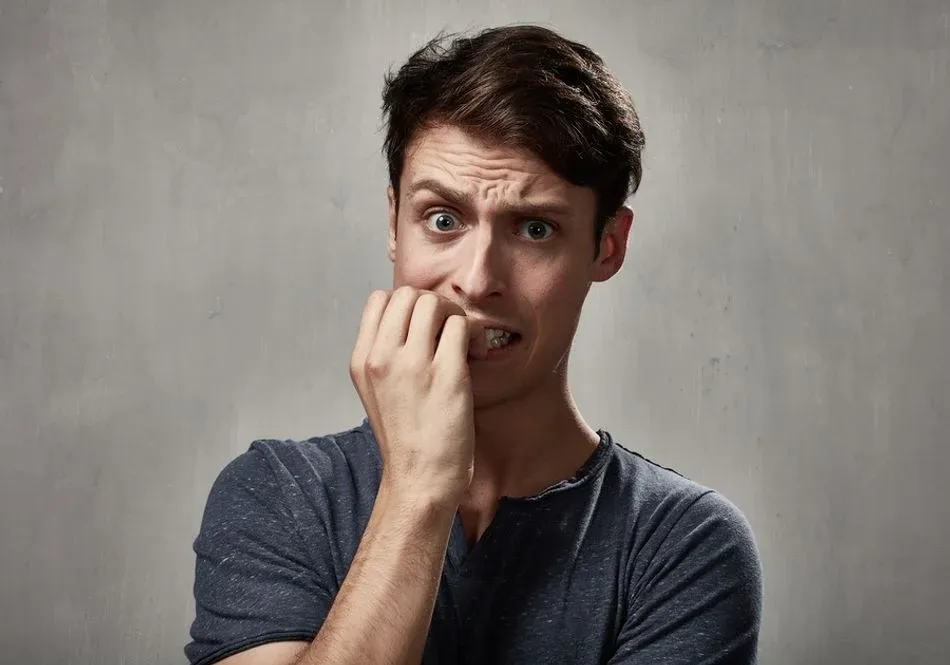
Do companies know what makes them successful, or are they just following the trend? Let鈥檚 dive into the current state.
Major companies like Boeing and GE have already adopted this change in their manufacturing processes and witnessed the benefits. Many CAD-vendors are also heavily promoting their new MBD features (at an extra cost).
In some industries, it can be used, but for example for (sheet) metal fabrication there are still some challenges which we鈥檒l look into right now.
The standard has gained maturity, but the market (CAD vendors, CAM vendors and manufacturers) isn't up to speed yet.
The exchange of CAD data in the new STEP AP242 format does not appear to be without problems. Some common features of sheet metal products are not (yet) supported and there is some resistance in the market to change.
The problems and issues
MBD is disruptive
With every disruptive technology there will the resistance, and there will also be many vendors jumping on this new trend selling their newest software.
Most often than not, you probably will be tempted to buy expensive systems, which could be irrelevant or absolute in the near future.
There is also a chance that you're "forced" to buy software to work for certain companies (think government, military, aerospace) which can create friction in business relationships.
Resistance & lack of skill
With every new technology, an innovation gap occurs: what has been invented is commonly misunderstood by end-users and vendors.
If you ask your clients to send you MBD files, they probably don't understand what you mean yet. If you ask your software vendors that you want to support MBD in your process, chances are they also don't have the right solutions for this yet.
Because MBD seeks to drastically cut out the steps in engineering, production, and quality control processes, there might be confusion about the new roles.
Lack of maturity & strategy
When exporting a 3D solid model with PMI data to the STEP AP242 format, not all necessary information is ending up in the STEP file.
In some CAD systems, not all features can be attached to the model and sometimes the PMI data is not written correctly in the STEP file.
As a result, some information is lost or incomplete or not useful because most CAD systems are not mature enough and manufacturers don't have the necessary software to interpret the file format to the fullest extent.
Practical issues for sheet metal fabrication
A number of important characteristics of a sheet metal product cannot yet be universally recorded in the STEP AP242 protocol. Dutch consultant Ton Derksen has conducted extensive research and concluded the following list of missing features.
A STEP AP242 file cannot support standardized documentation for:
- Rolling direction or surface treatments
- Threads on tapped holes with standardized norms
- Engraving information, for example for positioning during welding.
- Bending parameters such as shortening values or tool selection
Because of these shortcomings, for the production of sheet metal products with one of these characteristics, an additional file will always have to be sent in addition to the STEP file to have a complete Technical Product Documentation (TPD) whereby the argument that you no longer need a 2D-drawing is not being kept up at this stage.
You may already have discovered this when requesting quotes on a web portal. These features are not supported or you must enter them separately and upload a corresponding drawing.
So, in short: you cannot rely solely on your 3D model just yet. It is still required to have 2D-drawings and complete documentation.
But it makes sense to start already!
Why? Having a 3D annotated model can significantly improve your production quality if implemented well, for example by giving workers on the shop floor a 3D-viewer with the parts and assemblies so they can look up details without requesting additional drawings.
Don鈥檛 ignore the costs!
The cost of MBE puts it out of reach of smaller companies. You need to have viewers and if you design them with your CAD system, you need to export/import the information.
The biggest obstacle will be having an integrated factory where the intake into your system (ERP/MES/CAM) should support the AP242 data and it should make it all the way to the shop floor (and back). Those projects are costly.
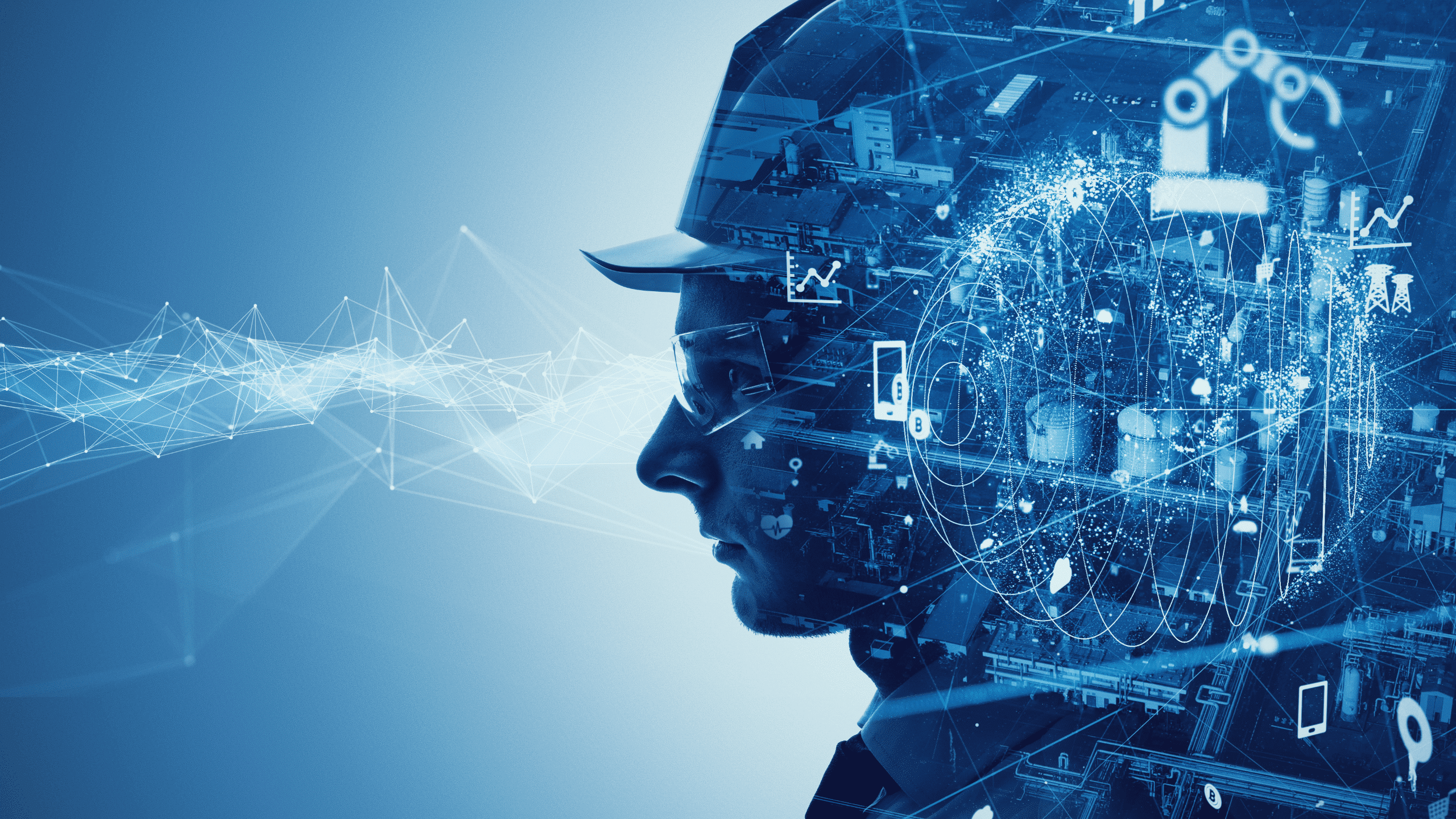
The future of MBD and PMI
There's a long way to go, but steady progress is being made and we can expect this to become a significant trend in the years to come.
MBD is a design technique that aims to make product design faster and more accurate. Traditional 2D drawings are the de facto standard for product design, but MBD may be something worth considering in the future.
MBD is already well applicable for specific industries like automotive, aerospace and medical equipment. For other sectors like construction and metal fabrication, it's work in progress. If you outsource work to subcontractors, those also must have the right software for this which often is not the case yet..
So, in summary: It is useful for some tasks, but it鈥檚 not very beneficial for the majority of them.
We might see this development continue and, in the near future, we might reach a tipping point. For now the metal fabrication market is not ready for it as of this stage.
So, Can MBE work?
Yes, it can. It has to be in a tightly controlled system that has little room for error. Everyone has to be on board and it will take time for the supply chain to mature in this regard, starting with the software vendors.
What we need for success with MBD
- Universal file formats must be widely accepted and used, with free export and free viewers.
- Files must be able to contain all necessary production data (Industry-specific support)
- Revision and history management in engineering documents
- Industry-approved validation processes (what if the engineer made a mistake with the PMI data)
- Easy conversion between machine-readable and human-readable formats (you don't want to still have to generate 2D drawings manually)
Also, if you include one non-compatible CAD or CAM system, the system has to be flexible enough to accommodate it. This limits your suppliers and increases costs.
Cost-effectiveness and commonality are the reasons for the development of new standard systems. The worst aspect of MBE is that it minimizes engineering definition, which is very problematic to the engineering process itself, where huge risks of failure can develop.
The way forward would be to urge major CAD companies to comply with market requirements. Form an industry board and define the standards for PMI deliverables that can be read by a readily available importer. Assure models can be delivered in a standard, compatible format.
It will be interesting years ahead.
How to get started today
If this made you excited about the technology, Take a look at some free viewers that are supporting MBD such as IDA-STEP, or the NIST analyzer tools.
The next step would be to define where and how MBD would work in your factory. For that, you'll need a clear strategy before starting the development.
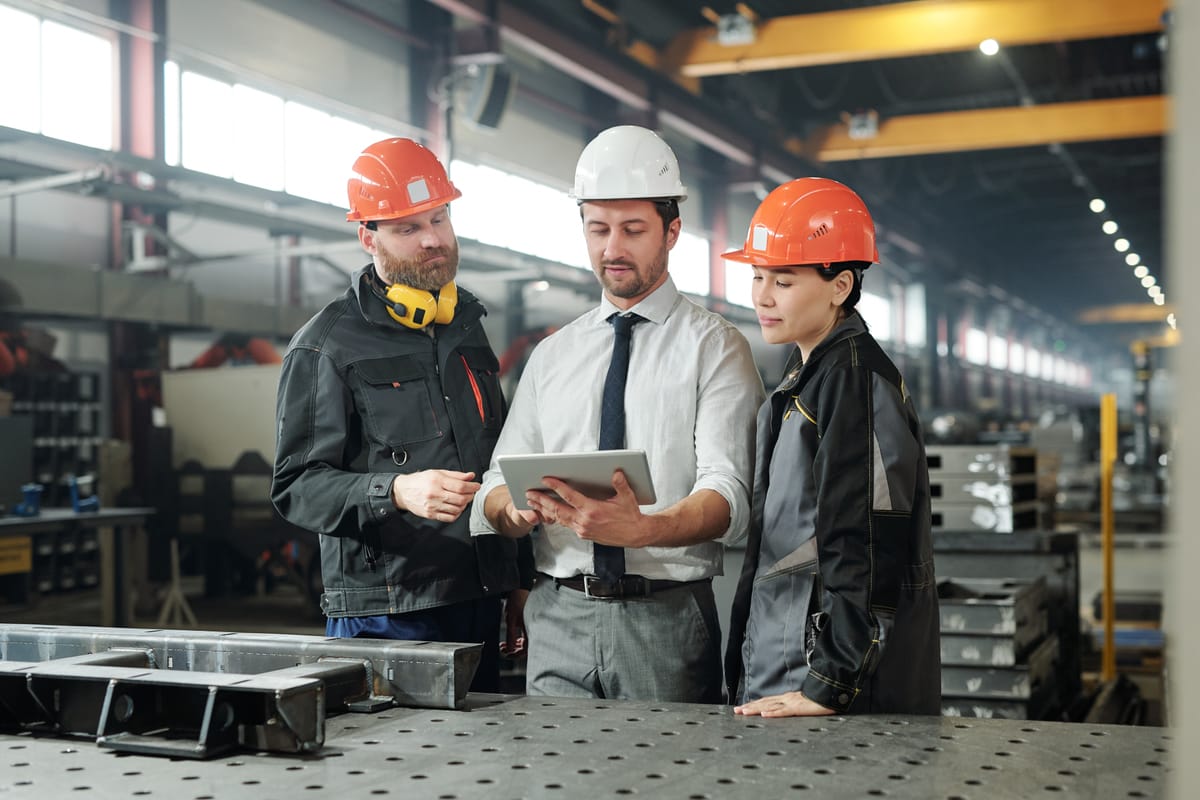